一、概述
近几十年来,汽车工程师一直致力于降低汽车排放技术的研究开发,并不断有诸如电动车、混合动力车及燃料电池车等低排放(LEV)或零排放(ZEV)车辆技术推陈出新。事实上,现今机动车辆的动力载体仍以汽油或柴油内燃机为绝对主体,只有降低内燃机汽车的排放才能真正缓解和逐步解决现行汽车排放污染的问题。降低汽车排放污染的课题主要分为如下三个分支,即内燃机燃烧技术(机内净化)、燃油品质及废气处理(机外控制)。
采用催化转化器是净化汽车尾气的重要手段之一,也是最有效的机外尾气净化方法。汽车批量装备催化转化器起始于上世纪70年代中期。其后,源自人类日益增强的环保意识而制定的各种愈加严格的排放法规推动了催化转化器技术的发展和普及。时至今日,催化转化器基本上已经成为降低汽车排放的强制性装置之一。催化转化器的核心技术主要集中在载体、催化剂和封装三个方面。其中,催化剂载体主要有陶瓷载体(Ceramic Substrates)和金属载体(Metallic Substrates)两大类。在此,本文将简要介绍金属蜂窝载体在汽车工程中的应用。
二、金属载体的发展历史
金属载体在20世纪60年代早期出现,至今已经经历了四个发展阶段,其产品技术也日臻完善(如图1)。
1. 第一代金属载体(螺旋状)
螺旋状金属载体是由光滑金属箔和波纹状金属箔螺旋卷绕而成的蜂窝式结构。由于当时的技术水平不能妥善解决其金属箔与金属箔及金属箔与外壳之间的紧固问题,所以最初的金属载体未能通过耐久性试验。其后,人们还尝试着加装十字架和固定销等一系列加强措施,但其耐久性仍不尽如人意。
2. 第二代金属载体(螺旋状)
第二代金属载体(产生于1978年)在第一代载体螺旋状结构的基础之上采用了高温焊接工艺,从而解决了芯体的固定问题,实现了金属箔与金属箔及金属箔与外壳之间接触点的牢固焊接。但是,第二代载体在试验及实际应用中出现了金属蠕变疲劳现象,从而大大降低了载体的耐久性。
3. 第三代金属载体(S型)
第三代金属载体(产生于1986年)采用了S型结构,成功地解决了金属蠕变疲劳问题。
4. 第四代金属载体(SM型)
为了达到高负荷应用条件的要求,基于S型载体的第四代SM型金属载体(产生于1991年)应运而生。SM型载体具有无可比拟的机械耐久性,可以应用于温度高于900℃和加速度大于80g的工况,从而在摩托车甚至赛车中开拓了新的应用领域。
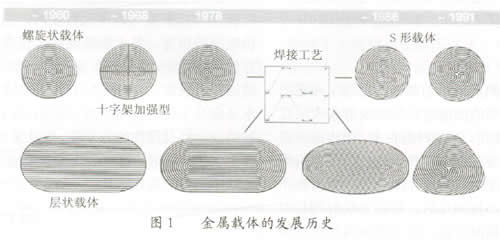
德国依米泰克(E m i t e c)公司是由西门子(SIEMENS)公司和纳铁福(GKN)公司各出资50%组建而成的合资公司,是当今世界上催化转化器领域最大的金属载体生产企业。截止2000年底,依米泰克公司已经累计生产了5,100万只金属载体。
三、金属载体与陶瓷载体的比较
直到上世纪80年代中期,汽车催化转化技术基本上完全依赖于陶瓷载体。由于近些年来世界性的汽车排放法规日趋严格,对催化转化器载体的性能也提出了更高的要求。金属载体由于自身具有低比热、壁薄及耐高温等优势而成为陶瓷载体的理想替代材料。
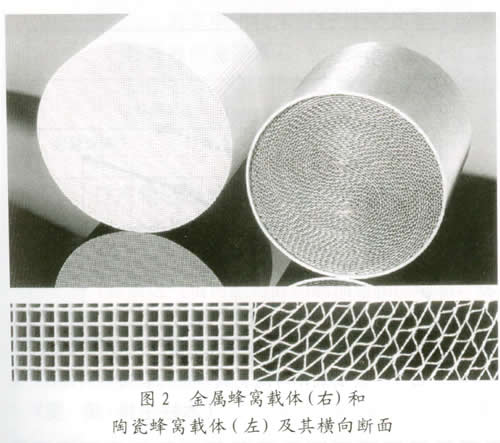
金属蜂窝载体可以用约0.04~0.05mm相同厚度的金属箔制成目数25~600cpsi的蜂窝载体。与同级的陶瓷载体相比,金属载体具有更为灵活的匹配性、更高的转化效率和发动机功率损失较小等优点。标准的陶瓷载体及金属蜂窝载体的主要区别如表所示。试验结果分析表明:
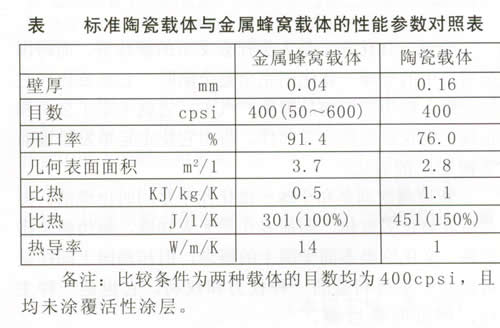
1. 采用薄壁(仅为陶瓷载体的25%)和特殊结构通道技术的金属载体拥有更大的几何表面积,即具有更高的转化效率。
2. 金属蜂窝载体具有更大的净开口率。载体净开口率的提高有利于减少压力损失(即降低背压),进而提高了发动机的动力性和经济性。
3. 金属载体存在50%的比热优势。金属材料的比热约为陶瓷的50%,综合金属箔具有更大的比重及陶瓷载体具有更厚的壁厚等因素后,金属载体仍具有较强的易起活特性。
4. 金属载体具有更高的热传导性。金属载体优良的热传导性有助于将载体上局部聚集的高热量迅速传递到与其相邻的结构上去,提高了转化器抵抗热冲击的能力,进而延长了转化器的使用寿命。
四、金属蜂窝载体主要的性能参数
1. 机械耐久性
应用在汽车工程(含摩托车)中的金属载体(尤其是当载体紧靠发动机排气歧管时)—直暴露在极高温度瞬变的条件下,其较薄的金属箔和较厚的外壳之间热膨胀变形差异就产生了较高的热负荷和机械负荷。另外,发动机的振动及气流冲击也显著增加了金属载体的机械负荷。所以,为了保证金属蜂窝芯体与金属外壳的牢固连接,其连接结构不仅需要具有一定的强度,还必须具备—定的韧性,以避免金属蠕变疲劳的发生。为了提高金属载体的耐久性,依米泰克公司先后开发了S型和SM型金属载体。

假设一个直径为90mm载体的中心部位温度比外壳部位高出250℃,利用有限元模拟算法FES(Finite Element Simulation)分析螺旋状结构和S型结构的结果表明:虽然该温度差使两种结构型式载体的芯体发生的变形均为0.073mm,但是其区别在于,螺旋状载体的最外层金属箔承受了全部的变形张力;而S型载体将变形扭转传向芯体中心部位(如图3),从而降低了芯体的局部张力。基于这种机理的螺旋状载体的试验结果如图4所示,出现了典型的芯体与外壳脱落的现象。大量的应用实例也证实了S型载体在机械耐久性方面明显优于螺旋状载体。
2. 背压
背压是衡量催化转化器性能的重要指标之—,背压的降低可以提高发动机的工作性能。背压主要受可供废气通过的净开口率的影响,而净开口率则主要由载体的壁厚和涂层的厚度决定。由于金属载体和陶瓷载体可以涂覆相同厚度的涂层,所以载体壁的厚度是决定净开口率的主要因素。也就是说,薄壁金属载体的净开口率要大于陶瓷载体,即金属载体具有较低的背压。
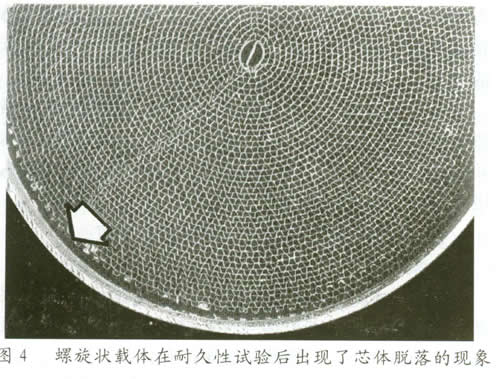
3. 几何表面积
几何表面积GSA是决定催化转化效率的三大关键因素之一。在相同的废气流速和同质同厚的催化剂涂层下,几何表面积越大则废气与催化剂的接触时间就越长,即催化转化效率就越高。图5为涂覆后的金属载体和陶瓷载体在不同目数下的催化表面积的比较。为获得相当于400cpsi金属载体的催化表面积,就必须安装相同体积,但目数为625cpsi的陶瓷载体。
4. 比热
金属材料的比热小于陶瓷材料,所以在相同几何表面积的前提下,金属载体具有比陶瓷载体更好的起活性能。
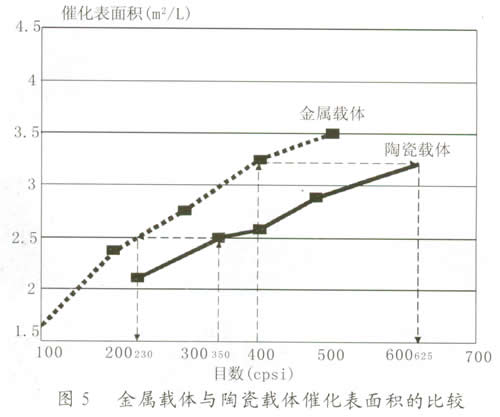
5. 目数
目数cpsi(cells per square inch)是指载体断面中每平方英寸所具有的蜂格数。例如,400cpsi = 62格/cm2;1000cpsi = 155格/cm2等。理论上在保持载体总体尺寸不变的前提下,提高其目数(即蜂格密度)就能扩大反应面积,从而大大增强催化转化器的转化效率。但在实际应用中,入口气体的温度和升温速度也会对转化效率产生重要影响。将金属载体催化转化器分别暴露在通过加热温度稳定在600K(代表底盘式安装)和700K(代表紧凑耦合式安装)的废气条件下进行测试的结果表明:在600K时,200cpsi的催化转化器的转化效率升高最快,而600cpsi最慢,在这一位置上,催化转化器的比热(热容量)是决定因素:在700K时则得到相反的结果,600cpsi的催化转化器的转化效率升高最快,这是由于在这种模拟的紧凑耦合式安装条件下,有足够的热量可被利用,所以较大质量或较大几何表面积的催化转化器能够迅速被加热到起活温度。详见图6所示。
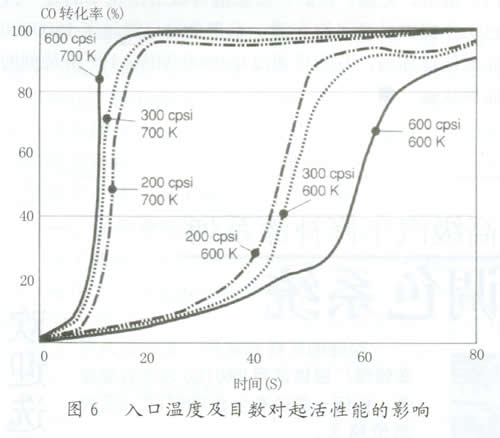
6. TS结构的影响
为了进一步提高金属载体的转化效率和缩小载体的几何尺寸,依米泰克公司推出了一种新型的横向凹脊结构(如图7)。TS结构是光滑金属箔和波纹状金属箔在横向经二次冲压处理形成的横脊结构。TS结构的应用可以使金属载体的体积进一步缩小10%。
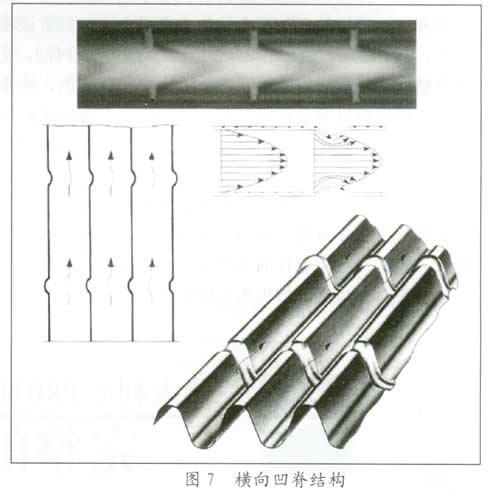
废气在进入传统载体的平直通道约5~10mm后开始变为层流,导致在管道内表面只进行有限的热量及物质交换。由于TS载体的横脊结构干扰了层流的形成,从而增加了通道内废气气流的紊流成分,即相应提高了废气与管道内表面积上催化剂涂层的接触面积和接触时间,所以TS结构具有更高的转化效率,试验结果证明了TS结构比普通结构至少高出10%的转化率。虽然,TS结构在增加气流紊流成分的同时也相应增加了背压,但是综合而言TS结构仍具有优势。其王要体现在如下两个方面:
(1)可以在体积不变的情况下减少金属载体的目数,从而增加功率、降低燃油消耗和成本。
(2)在保持目数不变的情况下,可以减少载体体积10%。也即可以降低贵金属的消耗量,进而成为最节省成本的方式之一。
五、金属载体在汽车工程中的应用
金属载体的低热容量(比热)有利于转化器的较早起活;其高热传导性有助于在发动机断火熄火的情况下保护转化器:较薄的金属箔材料利于降低背压和提高发动机性能;其较大的几何表面积结合TS结构可实现催化转化器体积的减小:其封装方式简单而又经济。基于上述这些特性,金属载体在汽车工程中的应用逐步普及并已经占有重要的市场份额。
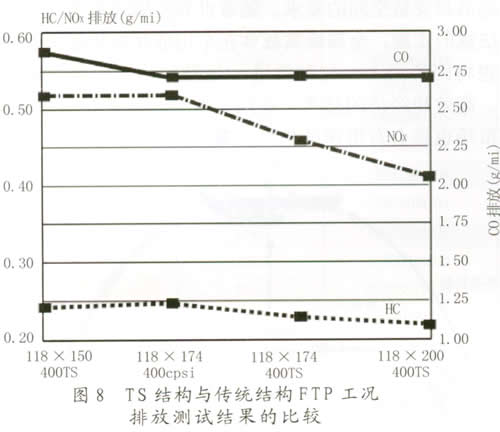
1. 金属热管的应用
依米泰克热管是将波纹状金属箔固定在金属外壳土,使其几何表面积增至圆周表面积的4倍(如图9)。由于热管不可能具有与蜂窝载体相同的几何表面积,所以其转化率较低。目前在金属蜂窝载体技术基础之上开发的适用于摩托车的热管技术,其最高转化率可达30%,可以满足不是很严格的排放法规的要求。同时,热管本身较低的成本及基体涂层和贵重金属的用量减少都相应降低了热管转化器的成本,从而为热管技术在摩托车工业中的普及应用奠定了基础。
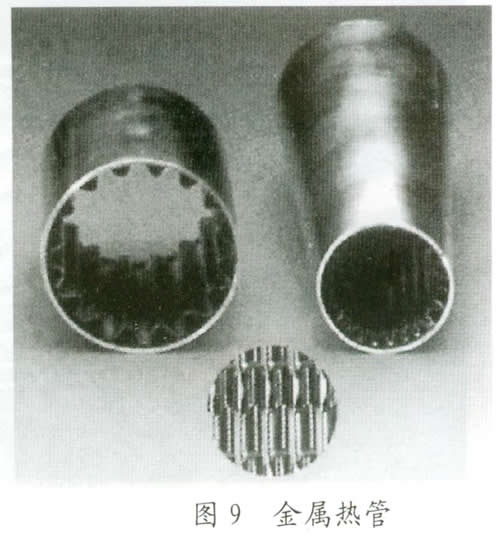
2. 金属蜂窝载体的应用
在实际应用及匹配过程中,使用何种类型的催化转化器主要取决于排放法规的严格程度,同时还需要进一步考虑安装空间、废气温度、原始排放等参数的要求。催化转化器在汽车上的装备主要有两种安装位置,即底盘式安装(Under-floor)和紧凑耦合式安装(Close Coupled Position)。催化转化器通常安装在底盘下(图10a),但该安装位置废气温度较低,起活性能较差。为了改善起活性能,在保留主转化器在底盘下的基础上,另外增加一个紧凑耦合式起活转化器(图l 0b)。为满足更加严格的北美和欧洲排放标准的要求,主转化器也采用紧凑耦合式安装(图l 0c),这种安装位置靠近发动机,废气的温度较高有利于转化器的较早起活,而且其转化器还较底盘式转化器更为紧凑。金属载体极为适合紧凑耦合式安装位置。
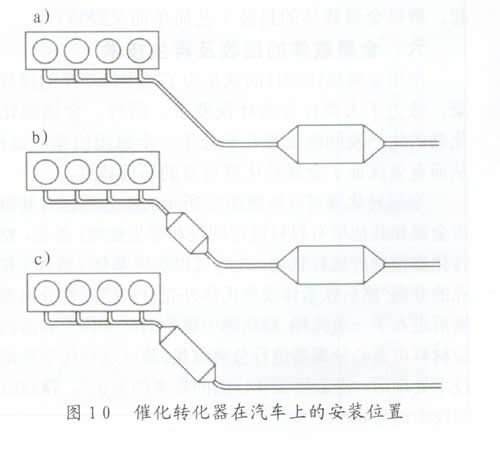
3. 电加热金属载体催化转化器
电加热金属载体催化转化器EHC(Electrically Heated Catalysts)能够显著提高发动机冷起动工况下的废气转化效率,进而被誉为1998年以来催化转化器领域最伟大的技术创新之一(图11)。EHC属于主动式催化转化器,其不受发动机和废气温度的影响,通过电气加热的方法达到要求的工作温度。在此,金属蜂窝状结构被用作电阻式热导元件。另外,辅助电池和高性能开关是EHC的基础装备。现在,EHC技术已经被宝马公司引入BMW V127系列车型中,可以超前满足未来对大型发动机更加严格的废气排放限值规定。
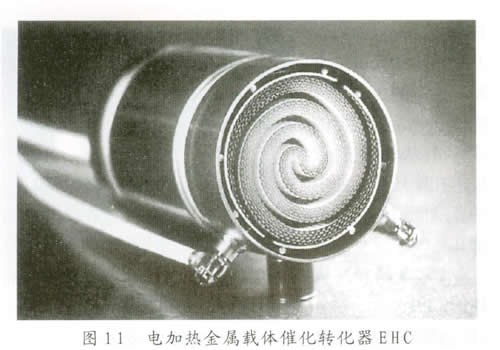
4. 金属载体的封装技术
金属蜂窝载体和热管由金属芯体或金属箔及由铁素体或奥氏体钢制成的外壳组成。外壳可以看作是封装过程的一部分,但是许多实际应用中需为转化器焊接足够的过渡管。为了避免焊接过渡管时对载体产生损坏,外壳外端面与芯体外端面之间应该留有约5mm的空隙。由于金属蜂窝载体和热管转化器与排气管可以直接焊接在一起,所以金属载体的封装工艺简单而又经济。
六、金属载体的回收及再生技术
应用金属载体的目的就是为了减少机动车的排放污染,致力于人类社会的环保要求。同时,金属催化转化器的生产及回收处理几乎处于一个封闭的循环过程,从而有效保证了金属转化器自身的环保特性。
金属转化器可以按照图12所示的工艺流程对其组成贵金属和其他所有材料进行回收和再生处理。首先,整个转化器被粉碎成粒状物,此时可以实现基体(载体)和外壳的分离;然后铁素体或奥氏体外壳材料经磁性分离器分离后进入下一道流程;粒状物中包含的从基体上剥落的涂层材料由离心分离器进行分离收集。通过这种化学和熔炼技术处理后,贵金属铂(Pt)的回收率约为95%,铑(Rh)的回收率约为80%。
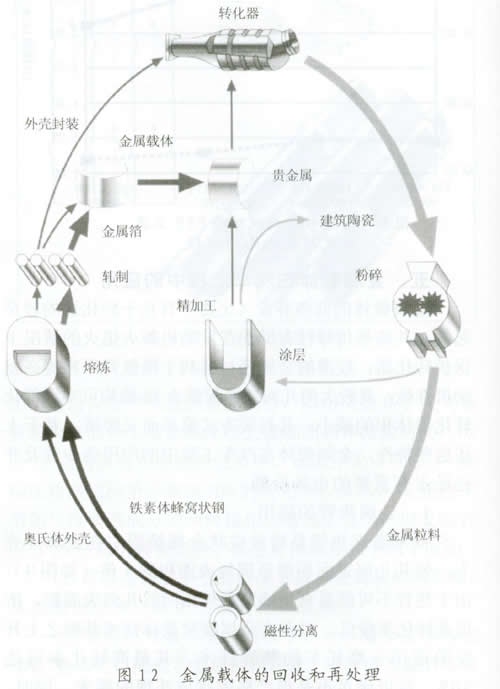
七、总结
排放系统中的催化转化器在使用过程中不断承受着诸如振动、热冲击、高温、水激冷及气流冲击等各种物理及化学负荷的影响,其应用环境极其恶劣。因而开发设计OEM催化转化器是一项复杂的系统工程,不仅需要借用现代的设计技术进行前期的设计分析、振动及流量分析、样品试制和模拟仿真等,而且在样品定型之前还必须进行热冲击、热振动、水激冷、发动机台架及实车路试等一系列系统严格的试验,从而有效保证匹配后的催化转化器能够满足对应千型的装载要求。
综上所述,金属载体的技术特性能够满足日前及未来排放法规的要求,特别是对于耐久性、排放稳定、早期起活和安装空间的要求。随着世界范围内更为严格排放法规的实施,金属蜂窝载体在车用催化转化器上的应用也将因势而上、与时俱进。另外,热管作为一种简单、高效和经济的技术,适用于限值较低的排放法规,其市场也将会有迅速的扩展。