周应军 俞庆伟
燕山大学
摘要 针对高速走丝线切割机易断丝的问题,提出了从钼丝的选择、机床的机械部分、绕丝、工作液、装夹工件、放电参数的选择、单边放电间隙、进给速度和停机等方面减少断丝的措施。
主题词 线切割机 断丝 措施
电火花线切割机为机械制造中某些特殊材料和特殊形状工件的加工提供了切实可行的方法,且我国的高速走丝线切割机在国际上独树一帜。但高速走丝线切割机的电极丝运动速度快(300~700m/min),且是双向往返循环地运行,在加工过程中极易发生断丝现象。因此对操作者的技术水平要求较高。加工过程中一旦出现断丝现象,不仅浪费钼丝,增加成本,还会影响工件的加工进度和质量,妨碍正常的生产。
切实有效地减少断丝的措施应落实到从准备加工到加工结束的每个环节中去。这主要包括以下一些内容。
⑴ 钼丝的选择
在满足加工要求的前提下,尽量选用粗一点的钼丝(例如直径可选Φ0.16~0.18mm)。这样一方面可以提高钼丝的张力(实际张力可达12~15N),减少钼丝的抖动;另一方面可以加宽切缝,使工作液容易渗透进去,有利于切缝中炭黑金属粉末排出工件之外。为了确保加工稳定,应及时更换损耗到一定程度的钼丝,避免因钼丝变脆断丝而中断加工。
⑵ 机床的机械部分
保持贮丝筒、导轮转动灵活,否则在往返运动时会增加走丝系统的惯性力,引起振动和断丝。绕丝后空载走丝检验钼丝是否抖动。若发生抖动要分析原因。如果因贮丝筒不同心或贮丝筒轴承、导轮及导轮轴承磨损所致,需及时调整或更换。挡丝装置中挡块与快速运动的钼丝接触、摩擦,易产生槽沟并造成夹丝拉断,因此也需及时更换。保证导电体与导电轮接触良好,否则高频电源负极无法与钼丝接通或接触不良,导致钼丝不能对工件进行正常的电蚀加工。而高频电源的自动控制信号仍使控制台的变频不断工作,步进电机继续进给,最后使钼丝磨、顶、夹断。保证工作液通道无阻塞,可使工作液保持一定压力和流量,具有良好的排渣能力和冷却性能。
⑶ 绕丝
钼丝要按规定的走向绕在贮丝筒上,同时固定两端。钼丝要拉紧,不能重叠。绕丝量可根据贮丝筒长短而定。一般来说,除两端各留10mm之外,中间尽量绕满,宽度不宜少于贮丝筒长度的一半,以免电机换向频繁而使机件加速损坏。
绕上钼丝后,调整挡丝装置,上、下挡丝装置都起作用,使贮丝筒上两边钼丝间距为挡丝销直径的1.5倍(约为8mm),见附图。绕丝完毕后,根据绕丝多少调整换向挡块的位置,一般两端各留2~3mm的钼丝不参加切割,以避免换向时发生断丝。
钼丝在加工一段时间后由于自身的拉伸而变松。当伸长量比较大时,会加剧钼丝振动或出现钼丝在贮丝筒上重叠,使走丝不稳而引起断丝。应经常检查钼丝的张紧程度,如果存在松驰现象,要及时拉紧。
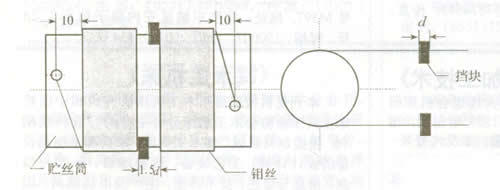
⑷ 工作液
及时更换陈液,保证工作液不能太脏,电蚀物浓度不能太高,使工作液保持一定的介电能力。尤其是加工硬质合金时电蚀物较多,使工作液的渗透性和流动性差,造成排屑不良。
⑸ 装夹工件
虽然线切割加工过程中切削力较小,但仍需夹紧工件,防止加工过程中因工件位置变动造成夹丝拉断。同时避免由于工件的自重,加上工件材料的弹性变形,造成夹丝拉断。
⑹ 放电参数的选择
根据加工工件厚度选择合理的电加工参数。将脉冲间隔拉开一些,有利于熔化金属微粒的排出。同时峰值电流和空载电压不宜过高,否则使单个脉冲能量变大,切割速度加快,容易产生集中放电、拉弧,引起断丝。一般地,空载电压为100V左右。在电火花加工中,电弧放电是造成负极腐蚀损坏的主要因素,再加上间隙不合适,容易使某一脉冲形成电弧放电。只要电弧放电集中于某一段,就会引起断丝。
⑺ 单边放电间隙
根据工件厚度选择合适的放电间隙。放电间隙不能太小,否则容易产生短路,也不利于冷却和电蚀物的排除。同时,放电间隙过大,将影响表面粗糙度及加工速度。
⑻ 进给速度
工作台进给速度如果太快,容易产生短路。在短路状态下,电流增大,钼丝极易变脆、老化,可能造成断丝现象。正式加工时,一般将试切的进给速度下降10%~20%,以防止短路和断丝。
⑼ 停机
应在换向后不久停机,防止贮丝筒因惯性超程冲坏传动件及拉断钼丝。