赵凯辉 魏朗
长安大学
[摘要] 以某EQ1208型车辆后桥鼓式制动器为例,对其三维热机耦合有限元模型进行了等速持续制动工况仿真。仿真结果与试验结果对比表明,仿真值和试验值在相同温度测量点的温升动态变化趋势相同,从而验证了仿真所利用摩擦因数温度特性的准确性。对该后桥鼓式制动器在连续15次循环制动工况下摩擦表面平均温度、摩擦副摩擦因数及制动管路压力的动态变化进行了计算分析。
[主题词] 鼓式制动器 摩擦副 摩擦因数
1 前言
当车辆进行连续较大热负荷制动时,制动器温度常在300℃以上,有时高达600~700℃。目前汽车上使用的摩擦衬片基本都是半金属摩擦材料,在制动过程中,随着制动器的温度升高,其摩擦副摩擦因数会不断减小,导致制动摩擦力矩显著下降,产生热衰退现象。因此,对制动器摩擦副摩擦因数在连续较大热负荷制动工况下的衰退值进行计算分析,有助于提高制动器工作可靠性,减少因制动热衰退导致的道路交通事故。本文以EQl208商用车后桥鼓式制动器为例,在等速持续制动工况下,对所建立的鼓式制动器三维热机耦合有限元模型进行了仿真,并与试验结果比较,验证了摩擦副摩擦因数温度特性的准确性;对EQl208商用车后桥鼓式制动器在连续15次循环紧急制动工况下摩擦表面平均温度、摩擦副摩擦因数及制动管路压力的动态变化进行了计算分析。
2 摩擦副表面温度
制动器制动时,由于摩擦副接触的不均匀性,实际接触面积远小于名义接触面积且不连续,其接触点的数目、尺寸大小除了与表面粗糙度、摩擦副材质的机械性能等有关外,还与摩擦接触面上载荷有直接关系。在弹性接触状态时,其实际接触面积、接触点数目与载荷成正比。摩擦时的热源首先在实际接触处产生,虽然热源在摩擦过程中将随着表面轮廓和实际接触面积的变化而改变,且其变化的特点和改变的程度取决于实际接触处的条件:速度、温度、载荷、摩擦过程中表层的物理化学变化特性、摩擦副材质的热物理性能及磨损状况等,但其中接触面载荷状况是最重要影响因素。对于鼓式制动器摩擦副,其接触面载荷呈正弦分布,因此在摩擦副中部载荷大的区域,其实际接触面积较大和接触点数目分布较多。
摩擦副在实际接触处的摩擦作用导致表面温度升高,接触面上载荷情况不同,各接触点热流密度也不同,其摩擦热流密度为:
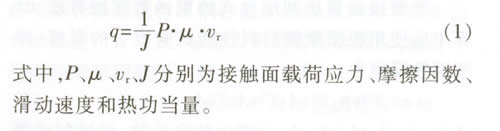
摩擦表面接触不均匀,使得温度分布不均匀,摩擦表面平均温度表明了摩擦副间的接触情况,可用于评定表层中所产生的各种变化,包括摩擦片树脂粘合剂的软化与分解
3 摩擦副摩擦因数
摩擦本身是一种动态随机过程,摩擦因数不是材料的固有特性,而是材料和多种因素影响下的综合特性,在各种影响因素中,尤以摩擦热及表面温升对材料摩擦性能的影响最为复杂,且尤其关键。在制动过程中,制动器摩擦副把汽车的动能转化为热能,当大量的动能转化为热能而又来不及耗散时,必然引起热量的累积和摩擦副表面温度升高,而摩擦表面平均温度对摩擦副尤其是有机摩阻材料的摩擦性能有很大的影响。通常,随摩擦表面温度的升高,摩擦因数会出现某种规律的下降,这是由于高温下摩擦副间表面膜的物化特性(树脂粘合剂的软化与分解)发生改变所致。一般制动器摩擦因数非线性温度特性如图1所示。
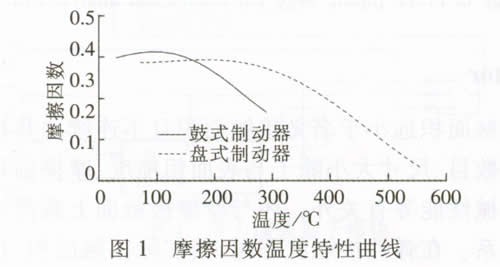


4 制动器摩擦因数温度特性验证
4.1 鼓式制动器三维热-机耦合有限元模型前处理
对导入ADINA的EQl208商用车后桥鼓式制动器装配体几何模型中各部件选择不同的单元组,各单元组统一采用3D-solid单元。对不同部件采用不同的材料属性,见表1所列。通过定义合适单元尺寸并进行实体自由网格划分,共生成5167个3D-solid单元。蹄、鼓接触属于刚-柔面面接触,在有限元模型中制动蹄摩擦片设定为柔性面,制动鼓内接触表面定义为刚性面。使用网格复制功能,生成5167个热传导单元。对流辐射单元通过定义对流辐射系数、对流辐射单元组,以及指定对流辐射面来生成。
4.2 主要约束及热边界条件
在等速持续制动工况下,制动鼓绕其轴线等角速度回转;两制动分蹄需能绕固定支承销孔轴线转动。
制动鼓作为制动器的主要对流换热部件,其对流换热系数h为:
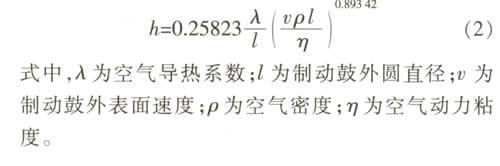
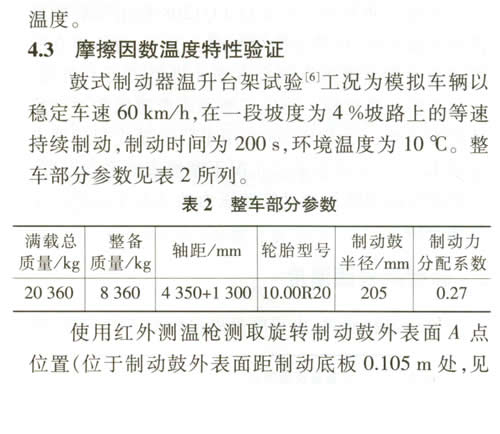
图2)附近温度,即为制动器温度。仿真工况与试验工况相同,利用软件耦合模块和ATS自动时间步长,对EQl208后桥鼓式制动器三维热-机耦合有限元模型进行仿真。图2为200s时刻瞬态温度场云图。因衬片与制动鼓摩擦副的接触表面压力按正弦分布,在接触面对应A点附近表面接触压力较大,摩擦产生热流量大、温度高,使制动鼓表面A点附近渗透温度也较高且温度梯度较大,同时在蹄鼓摩擦接触区温度明显高于非摩擦接触区温度。
图3中,在等速持续制动工况下,仿真温升曲线与试验温升曲线变化趋势相同,温度均随着制动时间增加而上升,因建模简化,部分非主要部件的散热和因素被忽略,随着温度升高,仿真温升曲线与试验温升曲线差值逐步变大。比较表明,制动器仿真值与试验值吻合较好,误差满足工程分析精度要求,耦合模型及在耦合仿真中所利用的摩擦副摩擦因数温度特性是准确的。
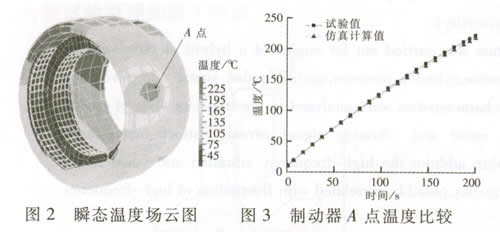
5 循环制动摩擦副摩擦因数分析
5.1 循环制动温度计算
整车循环制动工况见表3所列。参照行业标准QC/T 479-1999《货车、客车制动器台架试验方法》,对EQl208后桥鼓式制动器进行连续15次循环紧急制动温升计算。图4为15次循环制动的摩擦副表面平均温度循环曲线,图5是各次循环制动的摩擦表面最高平均温度。从图4和图5可见,经过15次循环制动,各制动循环瞬态温升和最高温度不断升高,最高温度升至330℃;各次循环制动的最高温升不断减小,表明制动器温度场达到生热和散热逐渐趋向动态平衡。
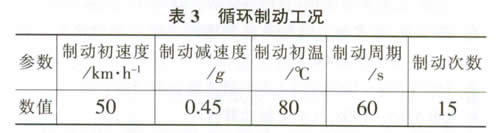
5.2 摩擦性能分析
根据各次循环制动最高平均温度及利用验证摩擦因数温度特性,计算得到各次循环制动中最高平均温度相应的摩擦因数。各次循环制动最高温度时摩擦因数动态变化曲线如图6所示。从图6中可知,随着温度升高,摩擦副摩擦因数不断降低且曲线斜率逐渐变陡,在第15循环最高温度330℃时,摩擦因数降至0.26。根据GB5763-1998《汽车用制动器衬片》对中、重型车鼓式制动器用摩擦副摩擦因数规定,在各次循环制动中摩擦因数均明显高于规定下限值,见图7所示。
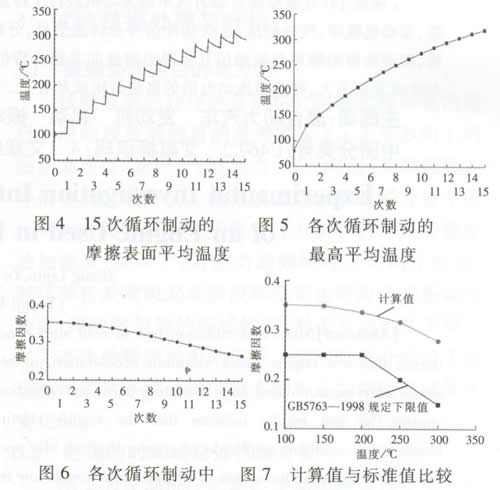
5.3 制动管路压力变化
制动器制动管路压力动态变化如图8所示。由于制动减速度不变,在循环制动过程中温度升高,摩擦因数降低,导致制动器制动效能部分热衰退,使得制动管路压力相应逐渐加速升高,在第15循环制动中,最高值升至690kPa。
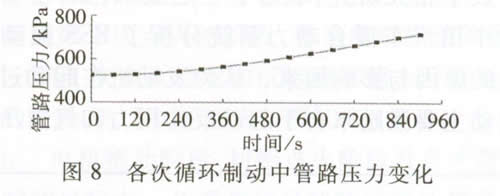
6 结束语
a.对所建立的EQ1208后桥鼓式制动器三维热-机耦合模型进行了耦合温度场仿真,并与试验温升结果进行了对比,结果表明两者吻合较好,验证了摩擦副摩擦因数温度特性的准确性。
b.利用所验证的摩擦副摩擦因数温度特性,对EQ1208后桥鼓式制动器进行了连续15次循环紧急制动温升计算。结果表明,保持制动减速度不变,随着各次循环制动最高温度增大,摩擦副摩擦因数不断减小且曲线斜率变陡,制动管路压力相应逐渐增大。