马继杰 吴博达 刘笑羽 程光明 孙景阳
吉林大学
王森林
信义集团
[摘要] 介绍了一种采用电动机进行能量补偿实现惯量模拟的方法,给出了能量补偿的数学模型。通过对飞轮的自由刹车曲线进行回归分析,得出由风阻和轴承磨损等引起的系统损耗模型。在NT11制动器惯性台架上设计了正交试验,得出能量补偿法中几个关键因素(补偿时间、补偿起点、补偿终点和补偿结束条件)的控制规律。讨论了能量补偿法存在的局限性,并给出了解决方案。
[主题词] 制动器 台架试验 电惯量 能量补偿
1 前言
惯量是制动器惯性台架试验中的重要试验参数,惯量模拟精度直接影响试验结果的准确度。最直接的惯量模拟方法是机械模拟,即在主轴上安装惯性飞轮,使其惯量与车辆折算到轮边的惯量一致,通过电动机驱动旋转来模拟汽车行驶动能。但是,机械惯量必然存在级差,对试验过程中各种损耗引起的惯量误差不能有效补偿,难以满足新型台架的精度要求。James K T曾采用控制电动机转速的方法进行惯量电模拟,模拟精度较高,但并未对各种制动条件进行详细分析,且转速响应存在滞后。林荣会等人采用控制电动机转矩的方式实现电惯量,但控制的稳定性和精度不高。
本文提出一种惯量模拟的能量补偿法,通过控制电动机输出功来补偿待模拟惯量储存的动能,从而实现惯量模拟。
2 数学模型
首先假设车辆在制动过程中作匀减速运动,预测的补偿时间小于实际制动时间,然后从能量角度对制动器惯性台架进行分析。
对于纯机械惯量台架,制动器消耗的能量(即飞轮储存的动能)由电动机在制动之前提供,在制动过程中没有外部能量介入。而电模拟惯量台架不存在专门的储能机构(主轴和电机转子除外),制动时电动机持续做功,以提供制动所需能量。考虑到设备整体的经济性,电机容量一般不能过大,惯量模拟范围受到限制。一种行之有效的方法是在电惯量台架中引入储能机构,即在主轴上安装一定数量的惯性飞轮,构成机械惯量和电惯量混合模拟台架。这种台架所需制动能量由两部分组成,一部分是飞轮储存的动能,由电动机在制动前提供;另一部分是电动机在制动过程中根据不同控制策略(如转速控制方式、转矩控制方式和能量补偿法)补偿的能量。飞轮提供的能量所占比例越大,电动机补偿能量越少,电机容量要求越低。合理配置飞轮的惯量可以有效扩大台架惯量模拟范围及减小电机容量。混合模拟惯量台架的典型结构如图1所示。
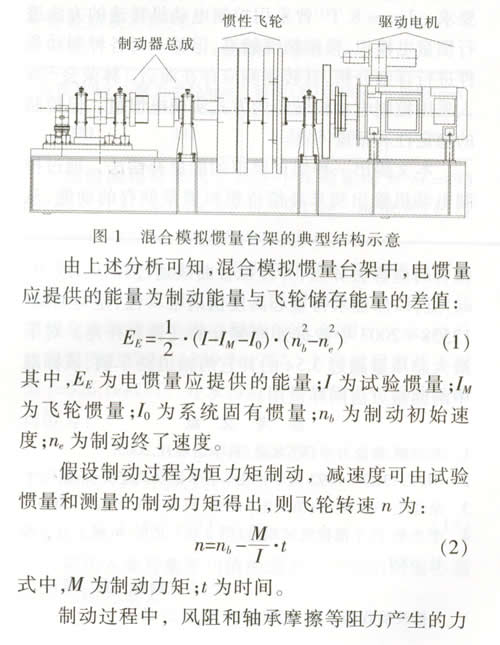
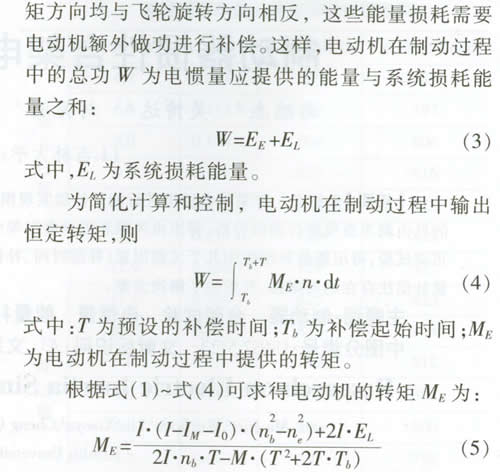
相同试验条件的制动过程,电惯量台架和机械惯量台架的制动距离应保持一致。恒力矩制动时,纯机械惯量台架作匀减速运动,制动速度曲线为一直线,如图2中直线AB。直线AB与两坐标轴围成区域的面积即机械惯量试验的制动距离。对于采用能量补偿法的电惯量台架,其制动过程由3段不同减速度的减速过程组成,即能量未开始补偿阶段(AC)、补偿阶段(CE)和补偿完毕阶段(EB),3段曲线下的面积之和应与直线AB下的面积相等。同一次制动过程中,安装的机械惯量和施加的制动力矩都是固定的,在没有外力作用的情况下,飞轮的减速度保持恒定。那么,直线AC平行于BE,且在安装的机械惯量小于纯机械惯量试验时,直线AC的斜率大于直线AB斜率;安装的机械惯量大于纯机械惯量试验时,AC斜率小于直线AB的斜率。于是,△ADC相似于△BDE,即要保证直线AB下的面积与AC、CE和EB 3线段下的面积之和相等,必须使D点为AB的中点,亦即△ADC全等于△BDE,由此可得补偿起始时间为:
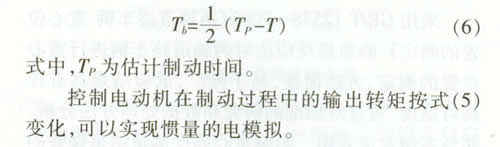
3 系统损耗模型
制动器惯性台架中的惯量误差通常包括飞轮的加工误差和风阻及轴承损耗等阻力引起的误差。飞轮的加工误差是固定的,可以在制造过程中加以修

将飞轮升速到最高转速,切断驱动电机电源,同时使制动管路压力为0,飞轮会在风阻和轴承摩擦等阻力作用下自由停车,停车过程中每隔15s记录一次转速数据,可以通过回归的方法得出纯阻力情况下的转速方程,进而计算出损耗方程。由于阻力的变化规律未知,不能按线性规律处理,因而试验要遍历各飞轮组合。通常,电惯量台架安装3个惯性飞轮,上述试验步骤要重复23次。
采用最小二乘法对曲线进行回归,回归过程用SPSS软件完成,本文仅对32kg•m2飞轮的转速回归过程进行分析。选取的回归模型为线性模型、二次模型和三次模型,回归结果如表1和图3所示。由表1和图3可知,测量数据中并不存在偏差较大的点,可以根据方程的判定系数进行选择。线性模型、二次模型和三次模型的判定系数R-square分别为0.997、0.999和1.000。三次模型的判定系数最好,但是后续计算量较大,线性模型判定系数又较小,综合考虑,本文选取二次模型为自由停车转速模型,则
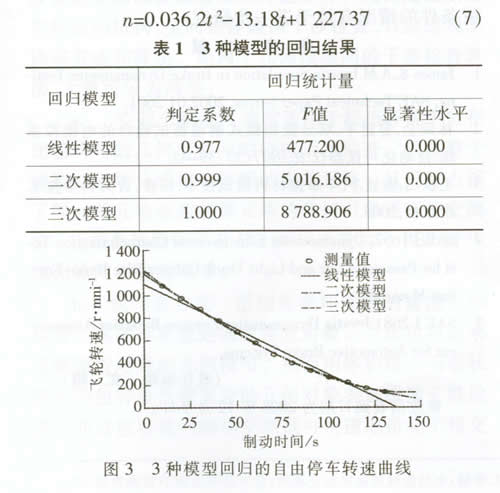
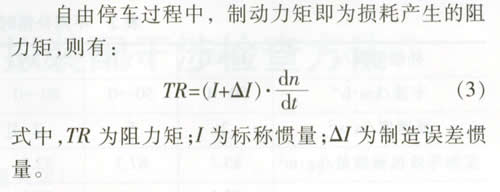
4 试验研究
为进一步确定能量补偿法中补偿时间、补偿起点和补偿终点等关键参数的控制规律,在NT11制动器惯性台架上进行了试验研究。
由于台架的电机控制器(6RA23)为二象限控制器,因此电动机模拟负惯量的情况暂未考虑。试验前,先用制动器将主轴卡紧,对电机的加载力矩进行标定。在利用电惯量和等量的机械惯量进行试验时,阻力作用的大小是近似相同的,为简化试验过程,本文对机械惯量和电惯量试验均不考虑阻力的影响(试验数据中实测机械惯量随制动条件变化而产生的误差正是由于阻力影响产生),以机械惯量数据为标准数据,与电惯量数据进行对比分析。
表2是补偿时间分别为估计制动时间的33%和66%时的惯量模拟数据。试验设定惯量为90kg•m2,机械惯量试验安装的飞轮惯量分别为90kg•m2、8kg•m2和32kg•m2,电模拟惯量试验安装的飞轮惯量分别为82kg•m2和58 kg•m2。由表2可看出,减速度为5m/s2、补偿时间为33%Tp,且电模拟惯量为32 kg•m2时惯量误差最大,而当相同条件下补偿时间为67%时误差明显减小。这是由于补偿的总能量一定时,补偿时间越短,电机应提供的力矩越大,加之试验中的力矩加载系统为开环控制,很难保证在整个加载范围内不受系统参数变化(如电机电枢电阻随温度变化较大,标定时难以保证预热到与工作状态一致)的影响。可见,补偿时间取值应在减速度较小且模拟惯量较小时减小,而在减速度较大且模拟惯量较大时增加。通常,补偿能量、补偿时间和制动距离均可作为能量补偿的结束条件,由于试验条件的限制(制动距离的测量需要专门提供的脉冲计数器),仅对补偿能量和补偿时间进行试验分析。
表3是采用补偿能量和补偿时间作为结束条件、电模拟惯量为8 kg•m2、补偿时间为制动时间的66%时的惯量模拟数据。由表3可知,补偿能量作为结束条件时,电模拟惯量的数据与机械模拟惯量的数据更接近,模拟效果更好。这是由于电机转矩加载系统采用开环控制,难以在整个范围内保持很好的线性度,当采用补偿时间作为结束条件时,控制器只是控制电动机在设定时间内输出恒定转矩,控制精度直接受电机转矩加载系统的影响。而采用补偿能量作为结束条件时,不论电机加载力矩是否有偏差,控制器都会控制电机按既定规律持续工作,直到补偿的能量达到要求的能量值,因而可以消除由力矩加载精度带来的影响。但是,如果加载力矩偏小过多,能量补偿尚未完成时制动过程已经结束,这将使电机出现短时堵转或制动结束后的短时升速,应加以避免。可见,在保证加载力矩标定正常时应优先选取补偿能量作为补偿结束条件。

5 局限性分析
采用能量补偿法实现惯量的电模拟存在以下不足,必须预先考虑:
a.惯量模拟范围受电机容量限制,电机容量过大势必增加系统成本,可以采用增加若干惯性飞轮提高惯量模拟范围的措施。
b.补偿时间的计算需要依据预测的制动时间,由于制动衬片的摩擦因数是随温度和压力等条件变化的不确定量,因而制动时间很难精确预测。当补偿时间与补偿起始时间之和大于实际制动时间时会出现补偿不完全的现象,因而应该使补偿时间在允许条件下尽量缩短。
c.采用能量补偿法模拟惯量势必使转速曲线变为折线形(图2中的折线ACEB),而且仅当补偿时间恰好等于实际制动时间且补偿起始时间为0时,转速曲线为一条直线。补偿时间越长,转速曲线越接近直线,但这与上述补偿时间尽量缩短相矛盾,因此折中的补偿时间取值范围是预测制动时间的50%~80%。
6 结束语
给出了能量补偿法的数学模型和损耗模型,并进行了试验研究。试验结果表明,能量补偿法是实现惯量电模拟的一种行之有效的方法,补偿结束条件宜优先选用补偿能量,补偿时间选取范围应控制在预测制动时间的50%~80%,补偿起始时间按式(6)选取可保证制动距离一致性。制动距离作为补偿结束条件的情况有待于进一步研究。