摘要
新的驾驶舱模块解决方案对机械、电子及功能进行了高度整合。在整个产品生命周期内,相对于传统的生产模式而言,模块化解决方案对提高生产效率与缩减成本方面都有显著的改善作用。此外,将驾驶舱模块所有零部件的前期物流、装配、质量管理与成品物流配送等生产进行外包,可为汽车制造商提供诸如最优的空间管理、高效的生产线配给、优化的生产线配置以及内在的质量保证等优势。
1.模块化已成汽车工业发展趋势
近年来,全球汽车制造商纷纷制定了以模块化为趋势,贯穿生产、市场、技术和财务等各环节的战略措施。
首先,对于汽车制造商而言,模块化可为其带来以下优势:
l 减少采购与供应链管理
l 缩短生产时间/减少单车生产所需劳动
l 降低保修费用
l 与模块供应商分摊研发和投资费用
l 与模块供应商分担研发和运营风险
而且,对于模块供应商而言,同样具有如下优势:
l 保持一级供应商的优势
l 获得复杂模块研发、装配与物流方面的核心技术
l 获得二级供应商的核心技术
l 提高价值链
总之,零部件模块化可大大节省生产整车所需的劳动力成本,简化生产工艺、提高效率和生产力,并允许汽车制造商与零部件供应商联合分摊项目的研发和集成费用。此外,不同车型使用相同的驾驶舱模块结构的案例,在越来越多的驾驶舱平台上得以实现,这一模式降低了开发和集成费用,使共享零件成本大幅降低。
事实上,驾驶舱模块外包的市场销售额已从2000年的16亿欧元,增长到了2005年的75亿欧元,并有望在2010年达到185亿欧元,其平均市场增长率高达25%。
2.基于卓越集成概念的驾驶舱模块
根据整车的概念,一个现代化的驾驶舱模块包括了防火墙与方向盘之间的所有部件,如横梁、踏板、空调箱、线束、仪表板等等,驾驶舱模块被看作是整车中最为复杂的工程模块之一(见图1)。
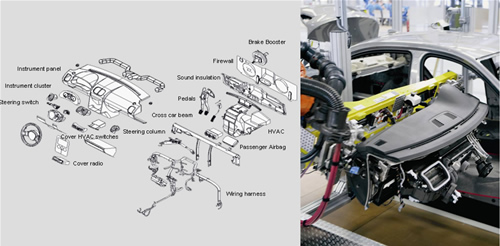
驾驶舱模块的构成
作为车辆与前排乘客的首要接触面,驾驶舱在功能性、舒适性和人机工程方面有着极其重要的作用。为同时满足技术规范、法律法规、客户需求及成本控制的严格要求,在车辆开发的初期阶段就应对模块化方案有所考虑。因此,在汽车制造商完成初始造型阶段之后,驾驶舱模块供应商就应加入到汽车制造商的研发团队中。
在过去,对于整车的研发,每一个零件和每一个模块都是孤立考虑的。如今,越来越多的汽车厂家开始考虑不同模块之间的协同性,并将其付诸于实际的操作中。汽车制造商希望通过一个驾驶舱模块平台制造出适用于不同车型的驾驶舱模块,其中的区别仅在于表面零件的不同。对于此类模块平台,要满足上述要求,就要求汽车制造商与驾驶舱模块供应商在车辆研发的初期阶段就开始考虑平台化与模块化的方案。
对于这种途径,驾驶舱的结构件必须被作为车型平台的通用件(见图2)。客户差异性仅存在于个别外观零件的不同,如仪表板、仪表板下护板、仪表、旋钮等。

驾驶舱模块平台涉及的外观件、模块构件及电气线束
对于驾驶舱模块化或平台化,市场上已经有一些成功的范例。例如,在C1平台上,福特Focus、C-Max、Kuga和沃尔沃S40/V40与马自达323共用相同的驾驶舱结构,实现了同一驾驶舱平台为三大汽车品牌提供驾舱模块。再如,雷诺汽车的Megane和 Megane Scenic车型,其驾驶舱模块的开发和系统集成工作,采用了完全外包的合作模式。
3.驾驶舱模块优化汽车配套产业链
对于一个现代的驾驶舱模块供应商而言,所需承担的责任将不仅局限于驾驶舱模块的装配环节,而是要对整个生产周期负责。将驾驶舱模块配送至汽车制造商,意味着模块供应商需担负起全部的供应商管理责任,其中包括质量管理、零件获取、零部件采购以及前期物流等工作。
为了实现驾驶舱模块的有效管理,需要驾驶舱模块供应商在主机厂生产线附近(不超过8km)建立自己的、独立的制造工厂,这也被称为“绿地解决方案”(见图3)。
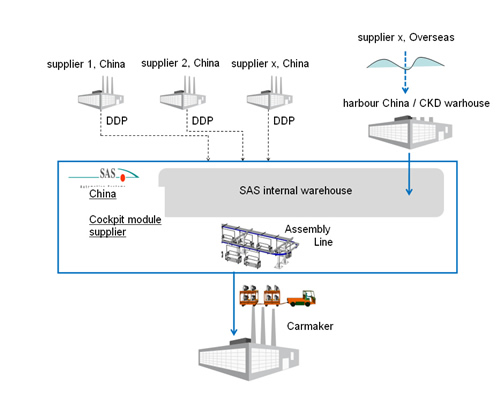
驾驶舱模块制造的“绿地解决方案”
在“绿地解决方案”下,形成了标准化的驾驶舱模块产业布局,其中包括优化仓库结构、优化内部物流流程、核定配给线、装配线平衡以及精确的排序配送JIS(Just-in-Sequence)。汽车制造商可提前制定出大致的车辆生产计划,并将其告知各级供应商。通过生产计划,主机厂、模块供应商和下级分包商能对生产前物流、原料周转与库存做出最优化、最准确的计划安排(见图4)。如今,优化生产的理念风靡全球,即便在JIS生产配送模式的要求下,只要模块制造工厂持有2-3天的平均库存量,也足以满足上千种组件的装配集成。此类集成供给结构大大缩减了驾驶舱模块供应商和汽车制造商的生产成本。
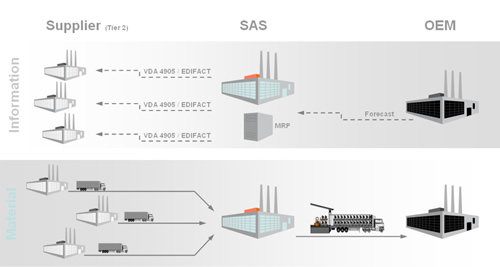
驾驶舱模块物流模式的原料周转计划安排
由单个驾驶舱模块供应商,依照“绿地解决方案”为汽车制造商供货的模式可为主机厂带来诸多优势:首先,合作的对象由供应商集群变为单个模块供应商,在质量管理方面主机厂可以完全依靠它们的模块供应商。其次,汽车制造商不需要再专注于单一零部件的质量问题,最终得到包含电器连接及功能测试,以及零部件装配间隙都合格的驾驶舱模块。二级供应商的质量问题、物流问题、驾驶舱模块层次内的问题,实质上不再是汽车制造商需要解决的问题。对汽车制造商而言,模块供应商的行为起到了“质量过滤器”的作用。
最后,并非最次要的一点,汽车制造商因制造车间场地有限引发的内部物流问题、生产淡旺季不均衡及其他各种日常问题,现在都可以通过“绿地解决方案”得到容易的解决。
结论
纵观全球汽车行业发展趋势,汽车制造商对模块供应商的倚重程度越来越大。整车中独立部分的研发生产可以被外包,使汽车制造商的成本大幅度减低,生产效率显著提高。将模块的相关工作外包给专业的供应商,汽车制造商便能专注于整车的研发与制造。
驾驶舱模块化所提供的全球性优势和机会包括研发、系统整合、前期物流、装配、质量管理以及JIS配送,将对汽车制造商的成败起到至关重要的作用。作为结果,主机厂将从系统集成到整车生产中获得长期利益和灵活性。
典型范例:
德国SAS汽车系统有限公司是法国佛吉亚与德国大陆集团于1996年以50:50股比组建的合资企业。SAS在全球率先开展驾驶舱模块的开发及组装业务,其客户覆盖几乎所有的欧美主流汽车制造商。2008年,SAS全球销售收入达29亿欧元,交付驾驶舱模块380万台。截至目前,SAS在全球建有21家工厂及9个技术中心。
SAS位于比利时Gent的工厂于1996年建立,现在主要为当地沃尔沃工厂的C30、S40及V50,以及XC60等车型提供驾驶舱模块。SAS Gent工厂约有200名员工,可满足24万辆车型的配套生产需要。2008年,Gent工厂销售收入1.79亿欧元。
除了提供技术服务、模块装配及排序配送外,Gent工厂还为客户提供前期物流服务,到美国、法国、波兰、土耳其、马来西亚、泰国及日本等分布在世界各地的零部件供应商处取货,并进行有效的库存管理。据悉,组成驾驶舱模块的大部分零部件由客户(如,沃尔沃)指定供应商,同时,具有强大同步开发能力的SAS公司也负责部分零部件的定点生产及采购,如金属支架、点火锁等。
在生产装配环节,Gent工厂采用了柔性生产线,以满足不同驾驶舱模块共线生产的需要。同时,在厂内零部件物流上,Gent工厂实施了诸多精益生产理念,最大限度地降低物料搬运距离、提高拾取零件效率,有效降低了生产成本。另外,在产品质量及性能检测上,Gent工厂也应用了大量先进的在线检测技术,以某款驾驶舱模块为例,在其产品下线前,以14台摄像头或数码照相机对其仪表板表面78个关键点进行照相对比,确保产品外观及装配质量100%合格。

德国SAS汽车系统有限公司比利时Gent工厂车间内景
作者简介:
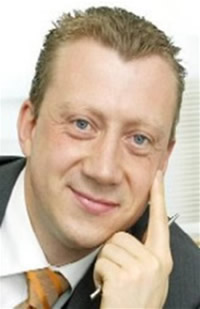
Karsten Brast博士,1996年毕业于德国亚琛工业大学,并于2001获得汽车塑料加工应用领域的工程学博士学位。Brast现任德国SAS汽车系统公司的工程副总裁,负责全球范围内的概念工程、产品工程、系统集成、工业化生产及项目管理。