后轮轮毂电机驱动电动汽车的液压复合制动系统匹配方法
宁国宝 王阳 余卓平
同济大学
摘要 根据某电动汽车的总体设计要求,提出了该类型电动汽车的液压复合制动系统前、后制动力分配和匹配原则,分析了后轮轮毂电机特性对液压复合制动系统设计的影响。以满足理想制动力分配为目标,利用非线性最小二乘法优化方法对该液压复合制动系统前、后制动力分配和匹配进行了优化设计,并在不同循环工况、整车质量及电机外特性情况下评估了优化结果。
主题词 电动汽车 轮毂电机 液压复合制动系统 优化设计
l 典型电动汽车电机驱动方案
图1给出了各种典型电动汽车的电机驱动方案。对比分析可知,轮毂电机驱动型式电动汽车不需要变速器、差速器、球型万向节、半轴等部件,其电机(电机+减速机构)直接放在轮辋里面,从而使结构紧凑且车身内部空间利用率高,整车质心降低,车辆行驶稳定性提高。传统车辆内燃机输出能量的10%左右在向车轮传递过程中会损失掉,轮毂电机驱动型式电动汽车由于动力传动链短(或者直接驱动车轮),而且能够通过能源管理和动力系统控制策略优化驱动、制动力分配,因而驱动系统效率高,能源消耗降低,提高了车辆燃油经济性。
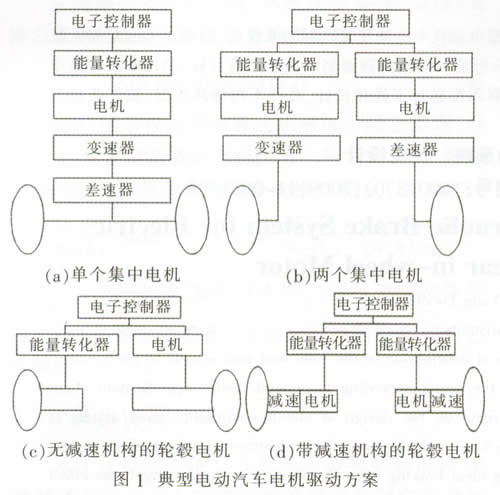
由于后轮轮毂电机驱动型式电动汽车的电机可以实现回馈再生制动,在制动工况下可以实现将整车动能转化为电能并存储,可明显提高整车的燃油经济性,同时由于车辆后轮增加了一个制动执行器,因此原液压制动系统容量(制动效能、制动热容量)均需重新匹配,以满足整车制动性能的要求。本文以某无减速机构的轮毂电机驱动型式电动汽车为对象,根据该类型电动汽车的总体设计要求,从复合制动设计角度出发,以满足理想制动力分配曲线为目标,提出该类型电动汽车液压复合制动系统的前、后制动力分配和匹配原则;分析后轮轮毂电机特性对液压复合制动系统设计的影响;利用非线性最小二乘法优化方法对该液压复合制动系统的前、后制动力分配和匹配进行优化设计。
2 液压复合制动系统设计原则
由于车辆后轮引入了可以实现回馈制动的轮毂电机,后轮制动系统增加了具有快速响应和实现正、负力矩输出功能的执行器,故该制动系统可以实现以下功能:满足驾驶员对制动力的需求;实现制动能量回收最大化:实现制动利用附着系数最大化,从而实现理想制动力曲线;提高制动时方向稳定性和舒适性。由于该类型复合制动系统设计是以制动器系统结构参数、电机特性和复合制动控制系统的控制参数为设计变量,以上述4点功能为目标的一个多参数输入、多目标输出的约束优化问题,贯穿车辆设计、试制、调试和标定各个阶段,具有一定的实施难度,因此本文仅从制动系统设计角度提出设计原则:
a.以实现理想制动力分配为目标,兼顾车辆的制动稳定性和舒适性。
b.在保证理想制动力分配目标的基础上,尽可能减少液压制动系统的容量,以减小整车的非簧载质量。
c.考虑到液压制动系统和轮毂电机的响应速度不同,以液压制动系统作为制动执行主体元件,以电机作为调节器,从而实现车辆前、后制动力的理想分配。
d.考虑车辆在不同载荷下制动系统的制动力分配特性,降低载荷对制动系统特性的影响。
3 液压复合制动系统模型
3.1 纯液压制动系统模型
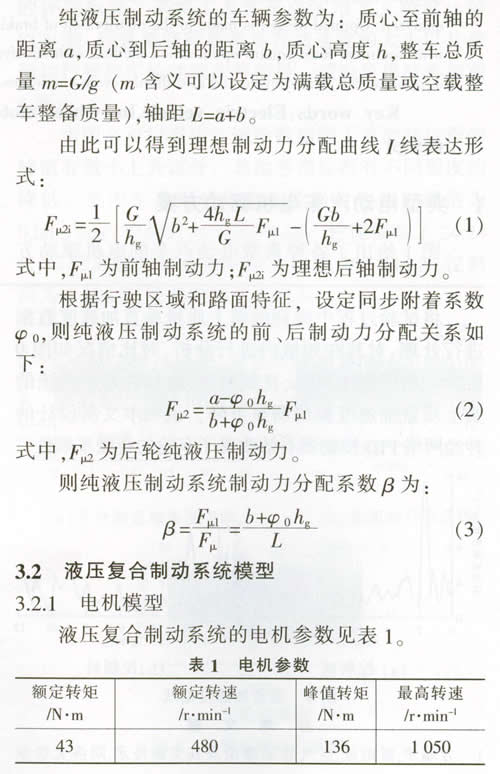
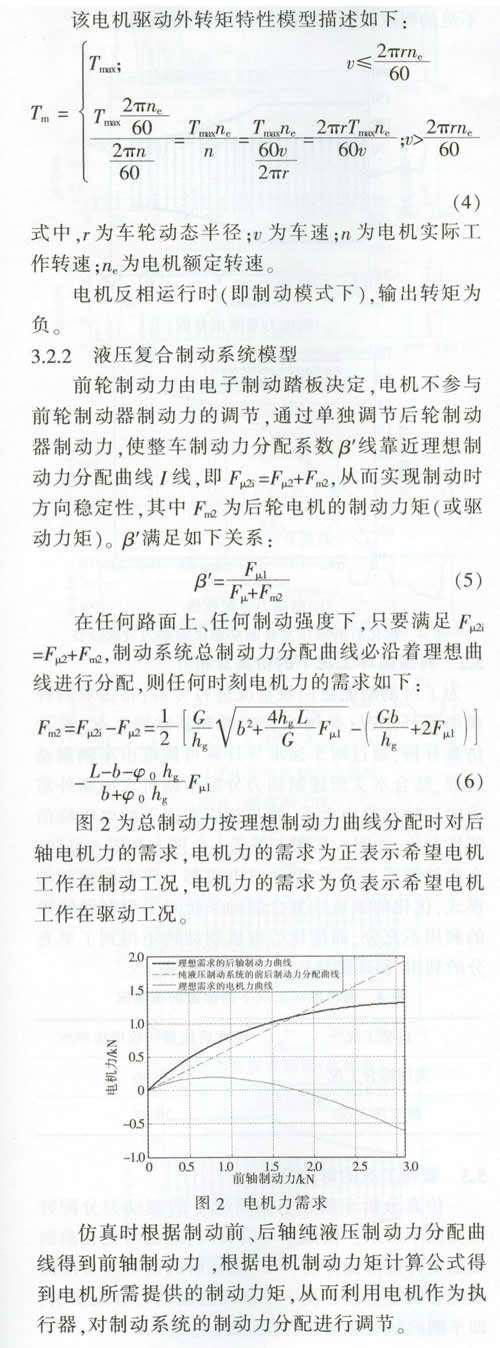
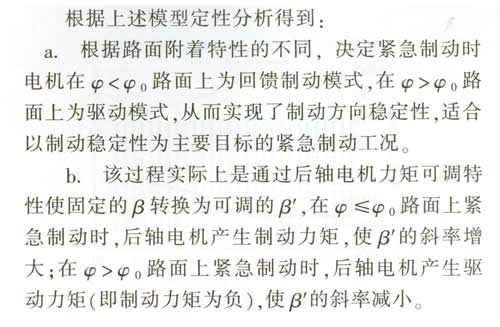
4 液压复合制动系统性能仿真分析
某后轮轮毂电机驱动电动汽车的整车部分设计参数如表2所列,工况参数如表3所列,该车纯液压制动系统的前后制动力分配系数为0.617。考虑车辆在不同车速和不同制动强度下对制动力的需求和满足情况,优化前的液压复合制动系统制动力分配特性如图3所示。图3a中两实线分别为电机在制动和驱动状态下随车速变化的峰值机械特性,阴影部分是电机在不同车速和不同制动强度下的实际力矩需求点。图3b中阴影部分为复合制动系统实际制动力工作点,在中小制动强度下,实际制动力工作点同理想制动力分配曲线重合。由图3可看出,由于未考虑轮毂电机的转矩特性,当轮毂电机作为辅助制动系统进行制动时,在中高速、大制动强度工况下电机驱动力矩不能满足需求,无法实现前、后制动力的理想分配;增大电机的峰值转矩特别是恒功率段的电机转矩,是实现理想制动力分配曲线的有效手段。
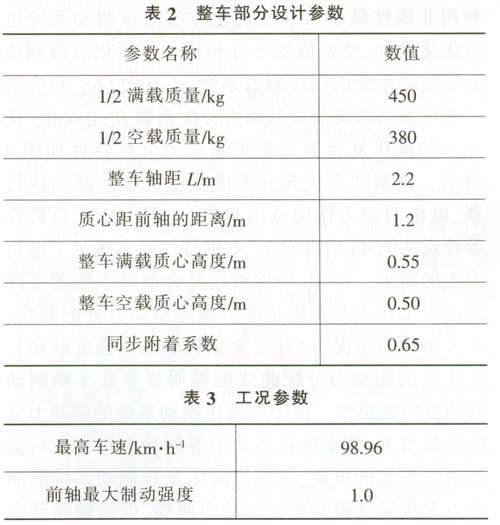
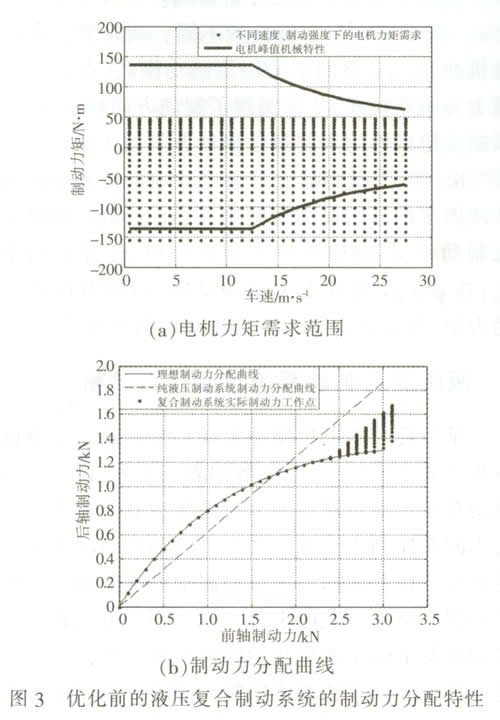
5 液压复合制动系统的优化设计与分析
5.1 液压复合制动系统的优化设计
以实现理想制动力分配为优化目标,同时兼顾车辆的制动稳定性,以同步附着系数为设计变量,依据车辆在不同车速(0,υmax)和不同制动强度(0,zmax))下的综合工况,形成以实际制动力工作点和理想制动力分配曲线差值为目标函数的二维矩阵,并利用非线性最小二乘法优化方法对该制动系统进行优化设计,使差值的平方和最小。优化后得到纯液压制动系统的同步附着系数φ’= 0.82268,对应的纯液压制动系统前后制动力分配系数β’= 0.660。优化后的液压复合制动系统制动力分配特性如图4所示,该制动系统充分考虑了电机作为制动执行器、电机制动力作用范围有限、电机力矩正负特性等特点从图4a中可看出,电机特性基本满足了电机力矩的需求,图4b中该液压复合制动系统的实际制动力工作点基本满足前后理想制动力分配曲线;在大制动力情况下(对应紧急制动或大强度制动),优化后的制动力分配曲线能够明显提高车辆制动时的方向稳定性。由于纯液压制动系统的制动力分配系数增大,使车辆在高速中等制动力时存在后轴制动力不足的可能,可能使液压复合制动系统的制动力无法完全跟踪理想制动力曲线,但后轴制动力不足的程度较低,对制动性能的影响较小。
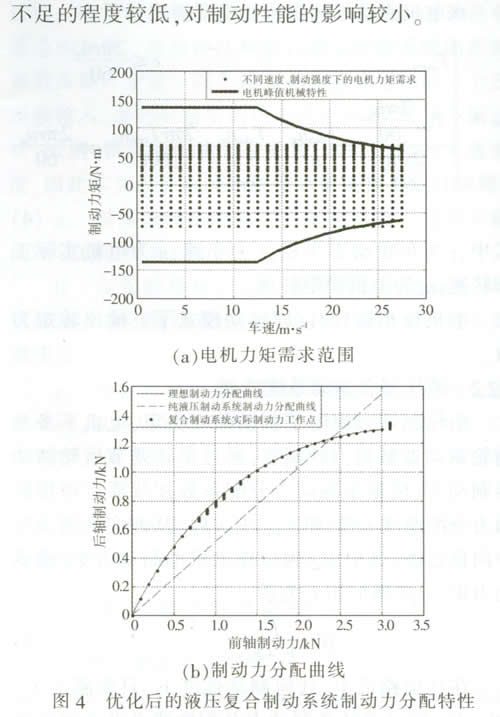
5.2 典型循环工况下的仿真分析
为了对制动能量回收情况进行分析,特选取两种典型循环工况(美国综合工况和新欧洲工况)进行仿真分析,通过对车速求导计算可提取出车辆制动过程,结合本文所述制动力分配策略可求出额外需求的后轴电机力大小,并与相应车速下的电机峰值特性对比,如图5和图6所示。由图5和图6可知,在两种循环工况下,制动时电机都工作在回馈制动模式,优化前该液压复合制动系统对电机制动转矩的利用不充分,而优化后电机制动转矩得到了更充分的利用,制动能量回收显著增加(表4)。
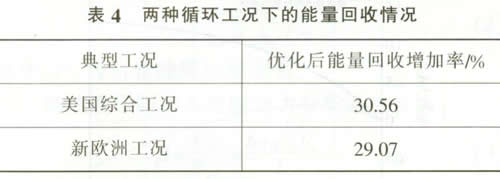
5.3 载荷工况的影响分析
仿真分析车辆在空载情况下的制动力分配特性如图7所示。由图7可以看出,通过与优化前制动系统特性对比分析可知,优化后的制动力分配曲线能够满足空载工况下车辆理想制动力分配要求,即车辆的制动稳定性明显提高。
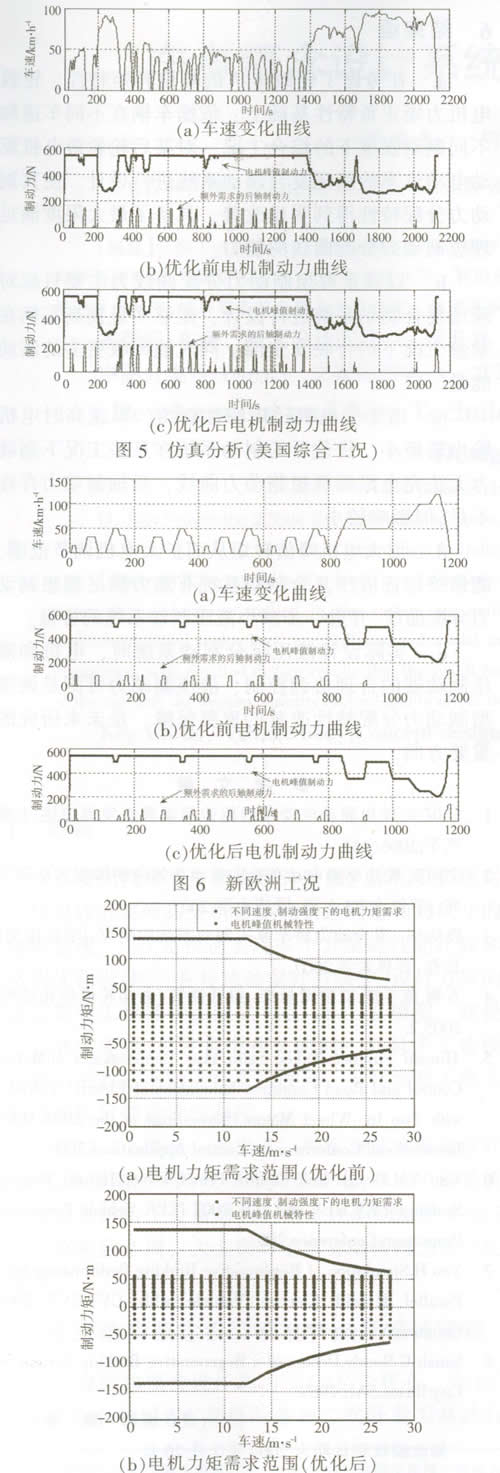
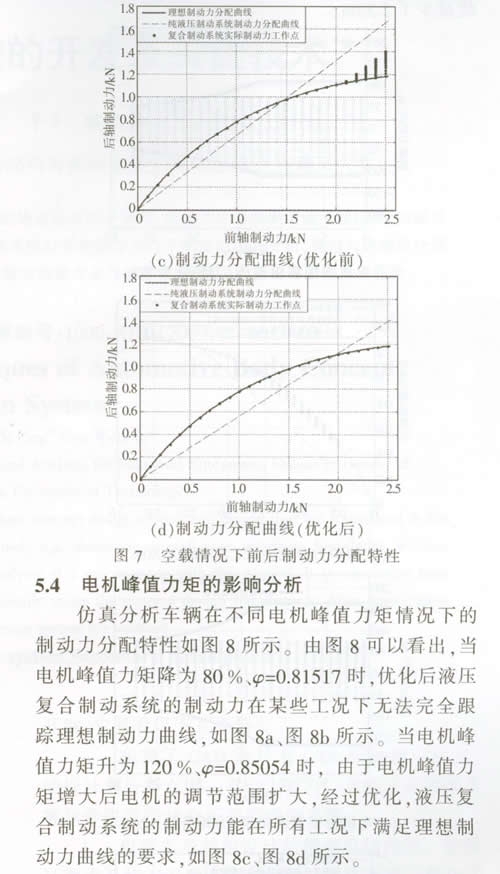
5.5 复合制动与ABS对比分析
利用Matlab/Simulink工具箱建立复合制动系统及车辆系统仿真模型,模拟制动时车速、轮速、制动压力等随时间的变化;用Simulink/Stateflow建立ABS控制器模型,实现ABS的逻辑门限控制,最后通过离线仿真,对引入电机后的复合制动系统和传统ABS以及车辆复合制动系统优化前后的制动性能进行对比分析。设计的试验工况为:紧急制动,良好路面状况,初始速度为98.96km/h,制动强度经过1 s增加至1,车速小于0.1m/s时仿真停止、ABS开启,结果见表4所列。由仿真分析可知,优化前复合制动系统代替了ABS的部分功能,车辆的制动效能有一定提升,车辆制动距离比纯液压制动系统减少了1.03m;优化后的复合制动系统能更充分地满足对制动效能的需求,车辆制动距离比纯液压制动系统减少了2.53m。
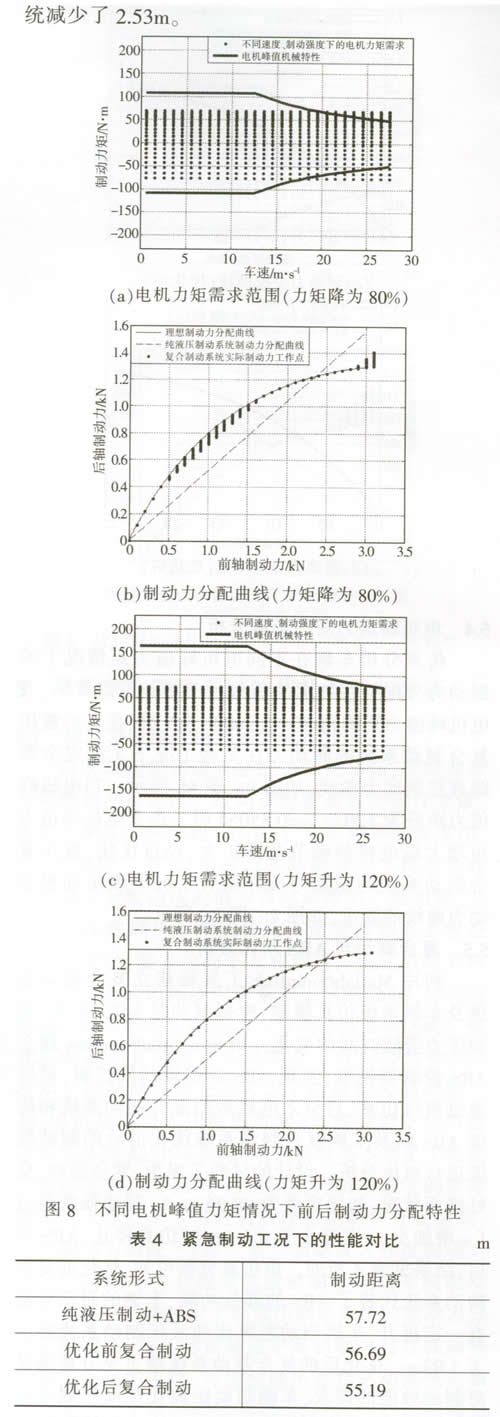
6 结束语
a.在考虑了轮毂电机的峰值转矩特性、轮毂电机力矩正负特性基础上,依据车辆在不同车速和不同制动强度下的综合工况,对某后轮轮毂电机驱动电动汽车的液压复合制动系统进行设计,使其制动力分配特性得到明显改善,具备了最大限度满足理想制动力分配曲线的能力。
b.以满足理想制动力分配曲线为主要目标对液压复合制动系统进行设计,能够明显提高车辆在紧急工况下的行驶安全性,同时能回收更多的制动能量。
c.由于受电机转矩特性制约,车速高时电机输出转矩小,优化后的制动系统在某些工况下制动力无法完全跟踪理想制动力曲线,后轴制动力存在不足,但影响较小。
d.增大电机峰值转矩从而扩大电机调节范围,能最终保证液压复合制动系统有能力满足理想制动力分配曲线,并进一步减小液压制动系统的容量。
e.实际设计液压复合制动系统时,电机和液压制动器的合理协调控制、液压制动力可测是该类型制动力分配特性改善的重要保障,是未来研究的重要方向。