车辆的制动性能是车辆综合性能检测中重要的检测项目,制动性能的好坏直接影响到行车安全和运输效率,做好车辆的制动性能检测尤其重要。制动试验台这种原来只在检测场才会出现的设备,现在也纷纷出现在维修企业中。
一、制动试验台的功能和结构
汽车的制动性能主要通过制动试验台,针对制动效能、制动抗热衰退性和制动时汽车的方向稳定性这3个方面来进行测试。制动试验台能迅速、准确和定量地显示出车轮的制动力、协调时间、阻滞力及驻车制动力,因而在维修和检测中得到广泛的普及应用。
制动试验台主要由4块平板、轴重传感器、力传感器和测量机构组成,它可以同时测量出车辆的前后轴轴重、各轮制动力和制动协调时间,以及左右两轮的制动力差等。
二、制动试验台的检验方法
检验员驾驶车辆以5~10km/h的速度,将车对正平板试验台并驶上平板,急踩制动踏板,使车辆停止。计算机自动测取各轮制动力、每轴左右轮在制动力增长过程中的制动力差、制动协调时间和各轮阻滞力,并测量驻车制动。制动试验台可以模拟真实道路情况,所得数据是在车辆行驶过程中测出的,能比较真实地反映车辆的制动性能。它的缺点是检测结果的重复性差,这是由于每次行驶的速度不同,踩制动踏板的时间不一样,造成车辆的惯性力不一样,因此测出的结果有一定差异。
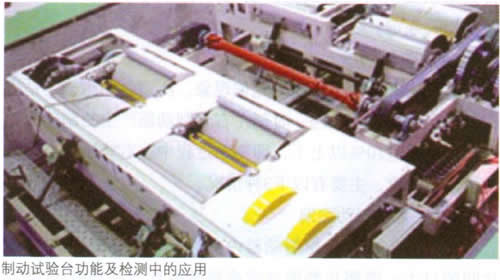
三、测量结果原因分析及案例
1.制动力小于规定值
根据国家有关法规要求,整车制动力矩应大于或等于整车重力作用下力矩的60%;前轴制动力应大于或等于轴荷的60%。造成制动力不足的原因主要有以下几种。
⑴ 制动器的技术状况
若某个车轮出现制动器内有油污、制动鼓/盘与摩擦片间隙过大、摩擦片磨损过度或新摩擦片与制动鼓/盘结合面不足等情况时,都将造成制动力不足。
⑵ 制动操作系统的技术状况
若出现下列情况,将造成某轴或整车制动力不足:真空助力泵膜片破裂或制动分泵密封圈损坏;制动液油管漏气、漏油;真空助力泵推杆变形或卡死;制动分泵活塞发咬;制动踏板有效行程过大;制动总泵漏油、漏气,推杆或活塞卡死等。
⑶ 其他情况
目前相关法规对后轴制动力并无具体要求,但后轴制动力不足可造成整车制动力不足。如依维柯等客、货车后轴装有感载比例阀,在空载检测制动性能时,感载比例阀未开户,制动力往往只有轴重的30%~40%;长途大客车或大货车因增加大型淋水器、工具箱等附属设施,造成汽车自重或后轴超重;轮胎磨损严重等原因亦可导致整车或某轴的制动力不足,,
案例:一辆长安奔奔1.3L轿车,在更换制动分泵之后进行竣工检验,在制动试验台上检测发现整车制动力为6510N•m,陔车整丰质量为1150kg,其60%重力作用下力矩约为6900N•m,通过数据分析来看,整车制动力不足。经过仔细检查,发现制动分泵密封圈在安装过程中损坏,将其重新更换后重新试验,制动力矩达到7000N•m以上,符合相关规定。
2.制动力差值过大
检测中经常会出现制动跑偏现象,所谓制动跑偏,是指在制动全过程中,在同一时刻左右轮制动器产生的制动力差值很大(超过10%以上),即制动过程中左右轮制动力增长的快慢不一致,主要有以下3种情况。
⑴ 紧急制动跑偏
同一轴上的某一轮制动器内有油污;制动鼓/盘与摩擦片间隙过大;摩擦片磨损过度或新摩擦片与制动鼓/盘结合面不足;真空助力泵膜片破裂或制动分泵密封圈损坏;制动液油管漏气、漏油;真空助力泵推杆变形或卡死;制动分泵活塞发咬;制动总泵漏油、漏气,推杆或活塞卡死;左右真空助力泵推杆长度不一致;某一轮胎胎面磨损严重等。上述这些情况都是紧急制动跑偏的重要原因。
⑵ “点制动”跑偏
汽车运行中经常使用“点制动”或“半脚制动”来降低车速。造成“点制动”跑偏的主要原因有:左右轮制动器内回位弹簧弹力不一致,使弹力大的制动器的制动力来得慢而回得快,造成制动初期和结束时左右轮制动力的差值过大。另外,制动系统联动机构润滑效果差、制动时左右轮动作不协调、某车轮的凸轮轴衬套和蹄片支承销发咬等情况,也会导致“点制动”跑偏。
⑶ “半脚制动”跑偏
紧急制动和点制动跑偏的因素同时存在,是“半脚制动跑偏”的主要原因。另外,同一轴某制动鼓磨损严重或失圆,个别车轮的凸轮轴衬套和蹄片支承销松旷等情况,也可造成“半脚制动跑偏”的现象。这在制动全过程中的反应为左右轮制动力的差值过大,而制动结束时的制动力差值不大。即汽车在“半脚制动”时跑偏严重,而紧急制动时跑偏相对较小。
⑷ 其他情况的影响
以下情况可导致汽车在直线行驶和制动时均出现跑偏现象:同一轴上左右轮轮胎气压、花纹、规格和磨损程度不一致,因轮胎的附着系数不同,制动力也不同;车架变形、前后轴弹簧钢板的U型螺栓松动、弹簧钢板中心螺栓折断等情况,都可能造成前后轴移位,即左右轴距差过大;前轮定位不正确将造成转向轮“发摆”、转向自动“跑偏”、轮胎异常磨损等。这些情况都将使汽车行驶和制动时的稳定性变差,直线行驶和制动时都跑偏。
案例:一辆桑塔纳2000GSi轿车,制动时向左侧跑偏,左侧车轮制动力矩为3500N•m,右侧车轮为4600N•m,二者差值已经超过10%,后来进一步试车发现直线行驶时车辆也会跑偏,于是进行四轮定位检测,检查发现前束与标准不符。重新调整前束之后,车辆恢复正常,在制动试验台上检验发现,制动力矩数值基本一致。
3.驻车制动力不足
造成驻车制动力不足的主要原因有:制动鼓磨损过度、失圆或制动盘有沟槽;摩擦片磨损过度;新摩擦片与制动鼓/盘结合面不足;制动鼓/盘内有油污;驻车制动操纵联动机构调整不当等。
4.车轮阻滞力过大
造成车轮阻滞力过大的主要原因有:制动间隙过小或调整不当;制动鼓磨损过度、失圆或制动盘有沟槽;制动总泵或分泵“咬死”不回位等。
四、设备对测量结果的影响
检测设备的精度和测控系统的稳定性,会直接影响检测数据的准确性和重复性,主要有以下几种情况。
1.制动力不足
制动滚筒磨损过度及滚筒或车轮表面有油污、泥垢等晴况,均可造成滚筒与车轮之间的附着系数下降,检测时制动力不足。
2.左右轮制动力差值过大
左右制动滚筒磨损不均匀,表面有沟槽或局部脱落,使左右滚筒的附着系数不—致,造成左右轮制动力差值过大,使检测数据的准确性差。
3.检测数据的准确性差
左右制动滚筒的制动力传感器线性差,设备标定时分段太少,以及左右制动滚筒不是采用同一标定点,这些情况都会影响检测数据。
4.准确性和重复性差
测控系统稳定性差,左右制动滚筒零点漂移大,会使检测数据的准确性、重复性差。
五、检测方法和操作规程对测量结果的影响
1.未采取安全措施
根据操作规程,制动性能检测时,应采取安全措施,在未检测的车轮后面塞三角木,以防止制动时车轮退出制动试验台。在检测装有储能弹簧制动装置的车辆时,常因制动力大并来得快,又没按规定塞三角木,使车轮突然向后退出制动试验台,造成测控系统采集不到制动力的最大值,设备显示制动力不足。
2.未能及时制动
驾驶员制动反应时间过长或制动踏板自由行程过大,可造成制动协调时间过长。驾驶员踩制动踏板力不足或制动踏板有效行程过大,均可能造成检测时车轮制动力不足,滑移率达不到要求,制动试验台不停机,车轮在滚筒上跳动。
3.制动踏板没有一脚到底
检测制动时,引车员没有按操作规程的要求把制动踏板一脚踩到底,而是中途回了一脚再踩到底,或由于制动踏板有效行程过小、制动管内有空气以及制动踏板力过大,使检测时引车员无法一脚踩到底,只好中途回了一脚再踩到底。这样可能造成检测数据不真实,放大了制动过程中左右轮制动力的差值。
4.操作不当使受检车退回制动试验台
检测车轮阻滞力时,若驾驶员操作不当,踩了脚制动或上制动试验台时速度过快,冲过试验台时第三滚筒或光电开关已启动,测控系统开始采集数据,此时受检车再退回制动试验台,均可造成车轮阻滞力过大。