夏捷 曹建永 王侃 景晶
国家机动车产品质量监督检验中心(上海)
制动器衬片不仅在安全性能上提高了要求,更在技术工艺上得到提升,我国制动产品虽然有国家标准、行业标准,但与国外齐全法规等先进标准相比,标准水平相差较大,不利于产品参与国际竞争,且现有的标准体系不健全,有较多的方法标准不完善。
在汽车工业迅猛发展的今天,汽车不仅成为国民经济的支柱产业,而且更多地走进千家万户,汽车制动安全逐渐成为影响人们行车安全的突出问题,制动器性能的好坏与制动器衬片的优劣有着直接的关系。因此为了保障安全,对制动器衬片的检测是必不可少的。国家强制性标准GB 5763《汽车用制动器衬片》第一次修订版于1998年开始生效,经过十年的发展,于2008年9月开始对《汽车用制动器衬片》进行修订。
本文主要介绍制动衬片在摩擦性能方面的修订。并结合我国产品现状和法规情况谈谈未来的发展趋势。
国际制动器衬片行业标准体系
国外制动、传动衬片(块)及总成标准主要有欧洲系列、美国系列、日本(日本汽车工业协会标准)和ISO系列,ISO系列主要参照欧洲标准制订。
美国标准主要有SA E、FMVSS、AMECA等;欧洲标准主要为法规如AK(如AK1、AK2、AK3、AKM)、ECE(R13、R13H、R90),EEC71/320;日本标准有JASO和JISD。
美国和欧洲标准又基本分为主机配套用标准,如FMVSS中的FMVSSl21、122、105、135及AMECA和R13、R13H及ISO11057,售后标准如SAE2430、TP121、R90及满足ECER13最低要求等。
ISO15484-2005(DIS)主要根据原全球规范而制订,引用了SAE、JASO、JIS D、ECE R90,并且规定了质量控制要求,是一个较完善的汽车摩擦材料标准。
目前,我国现行制动器衬片有效的标准且是强制性的只有GB5763。
我国标准发展现状
汽车用制动器衬片材料行业目前发展十分迅速。与行业快速发展的形势相比,制动器衬片的试验方法和评价方法严重滞后。GB5763-1998已经不能满足社会对制动器衬片安全特性的要求,并且国际上各主要标准法规也在不断修订。所以我国制动衬片的试验方法也在尽可能全面地适应这种变化,我国根据日本工业标准JIS D4411-1993《汽车用制动器衬片与衬垫》制定了国家标准GB5763-2008《汽车用制动衬片》,并于2009年9月10日实施,标准制定新的试验规范和评价方法,提高制动器衬片行业准入门槛,提高我国制动器衬片的产品质量,更好地对制动器衬片行业的发展起到督促和规范作用。
新标准主要修订内容
国标GB5763-2008的基本技术内容如图所示:
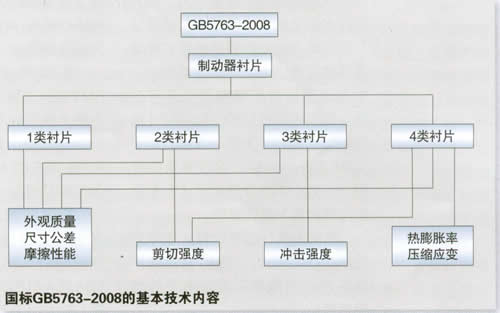
新标准在摩擦性能方面在原标准的基础上进行了修订,减小了相应的误差范围,提高了要求,并且新增了剪切强度、冲击强度、热膨胀率与压缩应变等试验要求,满足当前行车安全的需要。
摩擦性能。摩擦性能包括摩擦系数、指定摩擦系数的允许偏差与磨损率,是制动器衬片标准中最为核心的部分,也是标准中最为关键的指标,直接影响制动器衬片使用者的判断。
摩擦系数是直接影响汽车的制动性能,摩擦系数超过标准要求容易发生制动器抱死、方向失控或烧片,低于标准要求则容易发生制动失灵,易导致制动距离过长,不利于安全行车。而在汽车高速行驶中紧急制动时,摩擦系数过低就会出现制动不灵敏;摩擦系数过高会出现抱死现象,造成车辆打滑、翻转,对行车安全构成严重威胁。按照国家标准,制动器衬片适应温度为100℃~350℃。但许多不合格的制动器衬片,在温度达到250℃时,摩擦系数为0,这时制动就会完全失灵。这就给行车带来了相当大的安全隐患。
指定摩擦系数的允许偏差是指样品的摩擦性能是否达到了生产厂家承诺的要求,若不能保证产品摩擦性能的一致性,则会影响汽车的制动性能。购买同一品牌同一规格的制动器衬片安装在一辆车上,如果几块制动器衬片的摩擦系数偏差太大,势必造成制动不平衡,酿成车祸,造成对司乘人员的伤害。
磨损率则会直接影响制动器的使用寿命,产品不耐磨,缩短产品的使用时间,造成经济损失。此次新国标对于摩擦系数、指定摩擦系数的允许偏差与磨损率技术指标的修订,提高了原有的数值范围,增加了试验的难度。
在新国标的摩擦性能要求中,对1类~4类衬片的摩擦性能技术指标进行了修改。将1类衬片中指定摩擦系数的允许偏差“±0.12”修改为“±0.10”,磨损率“2.00、3.00”分别修改为“1.50、2.00”;将2类衬片中摩擦系数“0.15~0.70”修改为“0.20~0.70”,指定摩擦系数的允许偏差“±0.12”修改为“±0.10”,磨损率“2.00”修改为“1.50”;将3类衬片中摩擦系数“0.15~0.70”修改为“0.20~0.70”,指定摩擦系数的允许偏差“±0.12、±0.14”分别修改为“±0.10、±0.12”,磨损率“3.00”修改为“2.00”;将4类衬片中摩擦系数“0.20~0.70”修改为“0.25~0.70”,指定摩擦系数的允许偏差“±0.12、±0.14”分别修改为“±0.10、±0.12”,磨损率“2.50、3.50”分别修改为“2.00、2.50”。
同时,对1类~4类衬片所有磨损率的技术要求表达方式进行了改动,磨损率的数值由原先“小于等于某值”修改为“应从0至某值”。因为合格的制动器衬片既要保持适当的使用寿命,也不能受热后膨胀,所以磨损率不允许为负值。而旧标准对于磨损率数值的表达方式不够清晰,新标准该条款的修改可以使结果不再模棱两可,有利于对制动器衬片优劣的判断。
剪切强度。剪切强度是表征制动衬片与背板的粘接牢度,因为制动器衬片、制动蹄的粘切强度受温度影响较大,特别是在300℃以上的高温时,衬片与钢背的剪切强度非常低,如果汽车用制动器衬片剪切强度不足的情况下,就会造成制动器衬片材料内部分层,无法承受在制动时产生的剪切应力,必将造成“刹车失灵”。
由于2类和4类制动器衬片多是粘接型的,故需进行剪切强度试验。在新国标的剪切强度要求中,等同采用了国际标准ISO 6312:2001《道路车辆——制动器衬片——盘式制动块总成和鼓式制动器总成的剪切强度试验方法》,对2类和4类粘结型衬片的剪切强度的技术指标进行了说明,即在室温下2类和4类的剪切强度分别不小于1.5MPa及2.5MPa。
冲击强度。3类制动器衬片为中、重型汽车用的制动器衬片,属于铆接型的,则需要测定制动器衬片的冲击强度,如果冲击强度不够,在铆接时衬片会断裂,发生意外。
在新国标的冲击强度要求中,对3类衬片的冲击强度的技术指标进行了说明,即冲击强度不小于0.3J/cm2。
热膨胀率与压缩应变。4类制动器衬片属于盘式衬片,多用于小轿车或大巴车,在制动时如果压缩率和热膨胀过大,会引起抱死,所以需要测定4类衬片的这两项指标。
热膨胀检测,如果摩擦材料在变热时过度膨胀,在手刹制动后制动片一旦降温,会导致车辆滑动。新国标的热膨胀要求中,对4类衬片的热膨胀技术指标进行了说明,即热膨胀率(400℃±10℃)不大于2.5%。
压缩应变检测,确保其不太软而增加磨耗,也不太硬而导致制动系统振动。在新国标的压缩应变要求中,对4类衬片的压缩应变的技术指标进行了说明,即室温时不大于2%,高温时(400℃±10℃)不大于5%。
标准的不足亟需完善
制动器衬片作为汽车制动系统重要的安全部件,因其使用频率高而越来越受到重视。目前,制动器衬片不仅在安全性能上提高了要求,更在技术工艺上得到提升,我国制动产品虽然有国家标准、行业标准,但与国外齐全的ISO、SAE、JASO及欧洲的ECER、EEC法规等先进标准相比,标准水平相差较大,不利于产品参于国际竞争,且现有的标准体系不健全,有较多的方法标准不完善。制动衬片的检测今后应如何发展,国内很少机构或者相关部门进行书面、较详细的分析与论述,而未来的发展应着重于以下几个方面:
1. GB 5763是强制性的标准,对于制动器衬片的性能要求也只是最低要求,随着汽车制动器衬片产品向高性能化发展,仅考核制动器衬片的基本性能,如摩擦系数、磨损率、抗冲击强度等已不能满足发展要求,还要对制动振动、制动噪声、落灰等性能进行检测。
2.制动器衬片最重要的性能指标就是摩擦系数。在我国的国家强制性标准中并没有对摩擦材料使用的原料进行明确的限定,仅是要求成品制动器衬片安全性能必须达到一定指标。有些企业为了降低生产成本而在原料上做手脚。目前我国石棉制动器衬片在某些领域还占据着相当大的比例,尤其是在重型车制动器衬片市场。国外早已禁止使用含有石棉材料的制动器衬片,因此应对制动器衬片进行材料分析。
3.GB5763-2008设定的试验方法为小样试验,而目前为主机厂配套,特别是给国际市场OEM配套通常是进行台架试验,由于小样试验结果与台架试验结果无相关性,为了保证结果的相关性和国家标准的可行性,因此应对制动器衬片小样台架试验的研究。
汽车用制动器衬片质量的优劣直接关系到人民的生命财产安全,其重要性不言而喻。在满足了最低标准要求基础上,对摩擦材料进行全方位的开发研究,可通过标准研究来促进行业技术水平的提高,进而缩小与发达国家和地区的差距,使我国的制动器衬片行业能真正地达到世界一流水平。