新型FS浮式汽车制动钳创新及轻量化设计
葛宏 徐坚
上海汽车制动系统有限公司
【摘要】根据摩擦片的导向,在国际上主要有两种制动钳的设计概念,即德国大陆的专利产品FN制动钳(推拉式)和Collete制动钳(只推式)。FS浮式制动钳综合这两种制动钳的优缺点及创新设计,提出研发FS浮式制动钳的技术方案。
关键词:制动钳 汽车 轻量化
0 引言
汽车安全技术的研发是当前国际汽车技术发展的重要方向之一。汽车制动系统是汽车行驶安全的必要装备,制动钳作为汽车制动系统中的重要安全件,人们对它的要求也就越加严格。
目前市场上主流的两种制动钳,各有优缺点。推拉式结构制动钳虽然性能出众,但是加工复杂,质量较大,因此成本相对较高。主要运用在中高端的汽车上。只推式结构的浮式制动钳性能中等,质量也较大,但是加工相对简单,因此成本较低一些(如图1)。

1 FS汽车制动钳总成
研发具有卓越的安全性、舒适性、可靠性的汽车制动钳成为当今的发展趋势,FS浮式制动钳是为了适应这个发展趋势而设计的一款新型制动钳。
FS制动钳保留了摩擦片支架拉削式导向、活塞主动式回位以及带橡胶缓冲的导向结构,但是将推拉式的摩擦片导向改用了只推式结构,并以轻量化设计为主导思想设计而成。
FS制动钳主要设计要求及目的如下:优化功能,达到同类产品国际先进水平;保证质量及可靠性,满足国内外客户要求;改善制动舒适性,消除制动噪音及制动抖动等缺陷;降低产品重量,进行轻量化设计,目标减少15%重量;在优化功能及保证质量的前提下,实现成本优化15%。
由上海汽车制动系统有限公司自主创新设计的FS浮式制动钳产品,从概念设计、应用开发建模、有限元分析(FEM)到手工样件、台架试验以及道路试验,反复验证,实现了技术、质量、成本的统一。FS浮式制动钳切向力承载方式均采用只推式导向结构,不同于合资方德国大陆(Continental)公司普遍采用的推拉式导向结构,在保证制动性能的前提下,简化了部件的结构;尤其是FS浮式制动钳,设计概念中多处采用了减少加工量和简化装夹定位方式的优化设计,在采用拓扑优化设计诸如壳体和支架铸件的基础上,从加工工艺方面进一步有效降低产品的成本,同时保证产品性能不打折扣。
FS浮式制动钳内摩擦片采用的是主动式回位,也就是在内摩擦片背板上装了一个摩擦片弹簧夹,用来将摩擦片与制动钳活塞相固定(如图2所示)。制动完毕,驾驶员松开制动踏板后,制动钳活塞在回位时自动将内摩擦片脱磨,保证摩擦片与制动盘之间获得必要的盘片间隙。这不仅有助于减少拖滞力矩,减少行车时的行车阻力,同时还能减少摩擦片的磨损,保证其寿命。FS浮式制动钳上首次应用的V槽圆点加工定位方式,目前已经普遍应用到了SABS其他系列制动钳新开发产品上。它具有通用性强、定位精度高的特点,是产品设计结合工艺设计的一个很好的范例。
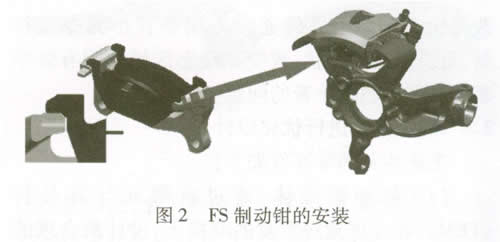
2 总体思路
FS浮式制动钳的工作原理是:汽车制动时,液压油通过进油孔进入制动钳,活塞推动内摩擦片对制动盘施加制动力,相对的,壳体受到一个反作用力的推力带动外摩擦片向制动盘施加压力,完成制动。
在现有制动钳设计技术的基础上,以提高制动钳的制动效能,简化结构,减轻重量,降低成本,增加寿命等方面为宗旨,基于产品的工作原理,按照如下思路设计方案。
2.1 零件公差校核
满足零件之间的间隙配合以及整车的安装配合,根据客户的整车布置条件及性能要求,用专业软件进行整车匹配,根据匹配参数设计并确定与其配套的制动钳结构及重要参数,包括设计新结构的壳体、支架、摩擦片、弹簧等。在此过程中,要对制动钳进行一系列的公差计算,来保证制动钳工作时不会产生零件与零件之间的干涉问题,例如:摩擦片与壳体、支架的干涉问题,导向销与支架、壳体之间的配合,活塞行程与壳体桥部、缸部的配合问题等。
2.2 轻量化设计
为增强制动钳结构稳定性,减少制动时的振动噪音和非正常磨损,优化壳体,支架设计保证产品性能、整体不变形的同时对制动钳壳体和支架进行轻量化设计。
通过有限元分析、模态分析和模态综合,分析出制动钳的壳体或支架振动频率和振型是影响制动钳稳定性、产生制动噪音和非正常磨损的主要原因,在保证制动钳性能的同时,优化壳体和支架设计,改变壳体和支架的质量分布、改变强度以及改善固有频率。另外通过采用噪音小的摩擦材料,更改其几何形状,改变非稳态区域的固有频率来解决客户制动噪音的问。
2.3 对零部件进行优化设计
主要涉及的零部件如下:
⑴ 制动钳壳体:通过有限元计算分析(FEM),在考虑减轻重量的前提下,设计最合理的壳体形状;
⑵ 制动钳支架:通过有限元计算分析(FEM),在考虑减轻重量的前提下,设计最合理的制动钳支架形状;
⑶ 制动钳活塞:钢活塞,首创氮碳共渗的表面处理方法。
另外对摩擦片、摩擦片保持弹簧、活塞、放气螺栓、壳体保持弹簧等小零件进行国产化,也能达到降低成本的目的。
综上所述,该项目的实施内容主要有:
⑴ 仿真分析不同壳体、支架形状对总成变形的影响;
⑵ 零件设计,包括设计新结构的壳体、支架毛坯,以及相关计算等;
⑶ 完整的台架试验对比;
⑷ 试验验证,包括各种台架试验和疲劳试验。
3 技术方案
3.1 只推式支架强度分析优化
FS浮式制动钳切向力承载方式为只推式导向结构,在保证制动性能的前提下,简化了部件的结构,同时它还具有装配简易、加工工序简单的特点,为降低成本要求引导了一条出路。然而由于受力结构的不同,只推式导向结构对支架的强度要求要远远高于推拉式导向结构的要求,这对于CAE应力分析和仿真计算提出了更高的要求。
有限元分析计算主要是分析支架在不同的受力模式下的强度及变形。以上汽AP11匹配项目为例,其支架为只推结构,受力模式为推动模式,内外侧各承力50%。计算结果显示,支架的受力情况最为严重的部位处于摩擦片导向槽靠外侧的圆角边处、安装孔凸台的机加工棱边处和台阶处。
根据计算结果如图3所示位置,由于受应力强度较大,需要修改模型来满足其支架结构的强度要求,作为验证,有限元再次对修改的模型进行分析计算。经过多次的计算分析及和对支架结构的调整与修改,最终满足了高速制动情况下的强度要求。
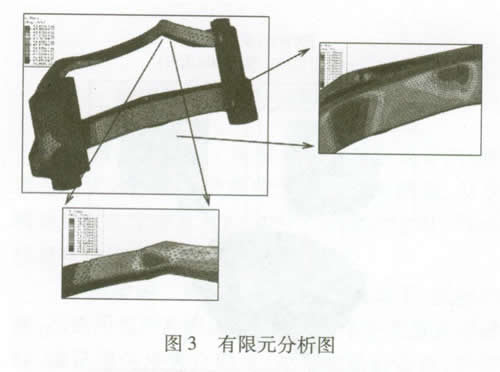
3.2 壳体支架优化设计及有限元分析
目标是保证产品性能、整体不能变形的同时对制动钳壳体和支架进行轻量化设计。采用拓扑优化方法可以使材料达到最合理的分布,应力分布也更加均匀。考虑到零件试验需要大量的模具投入,利用公司的有限元分析(FEM)能力;进行了一系列模拟工作。
3.2.1 不同轮廓的对比
基于现有制动钳模型,根据经验,设计了多种不同的壳体和支架轮廓,分别对壳体和支架进行了拓扑优化,使其在满足强度和刚度要求的前提下,进行轻量化设计,一方面对整体材料减薄,另一方面在相对薄弱点加固。图4为壳体和支架优化过程,图5为壳体和支架拓扑优化后的模型比较。
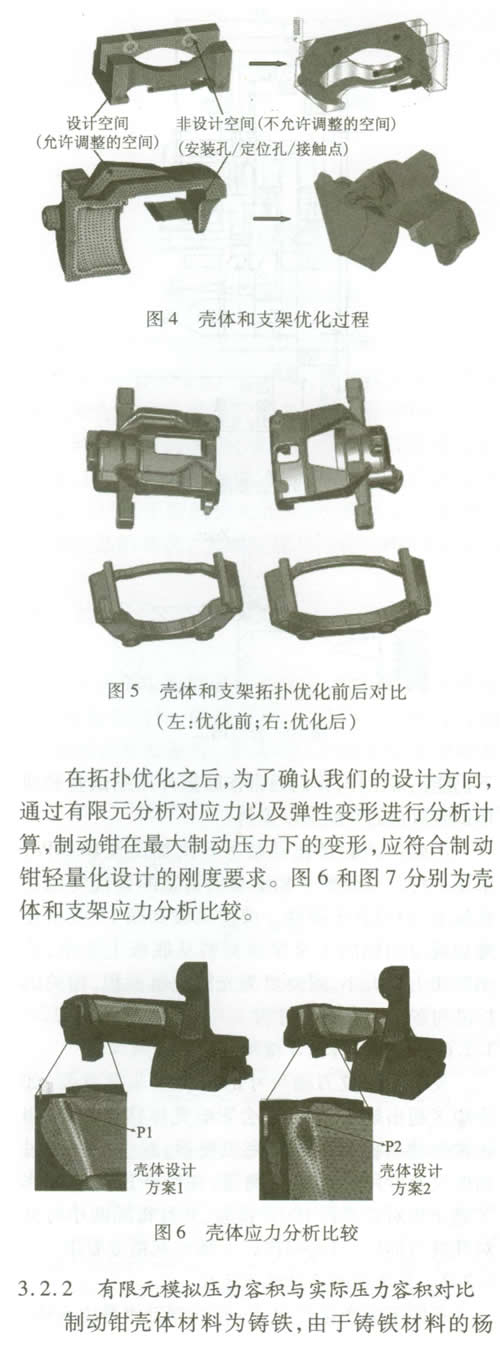
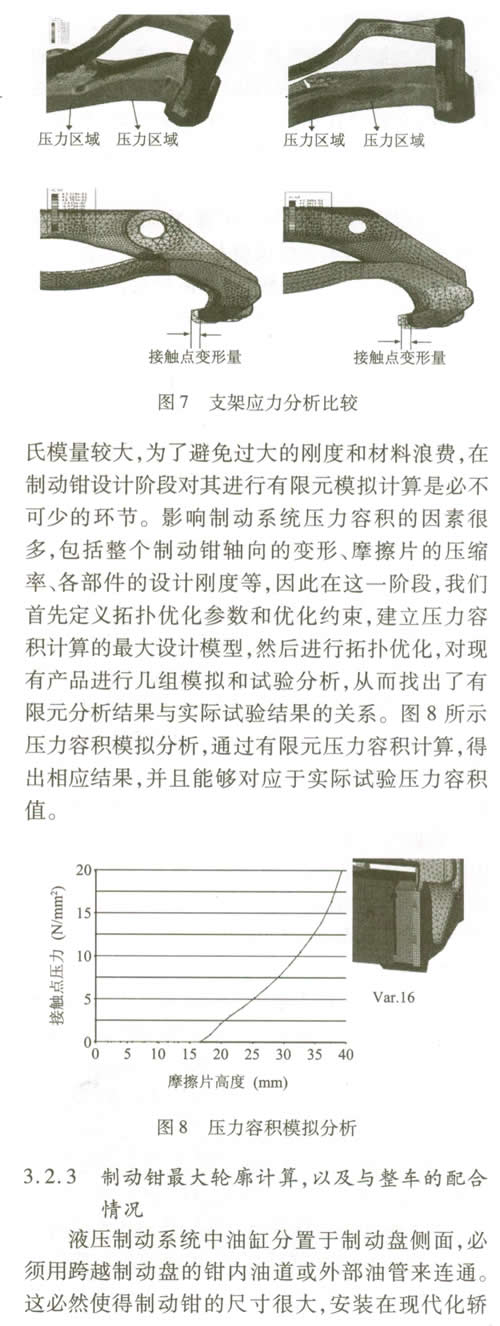
车的轮辋内则需要设计者深入的研究。
⑴ 根据客户提供的整车尺寸及布置情况,将所选型号的制动钳与客户提供的二维装配图纸进行比较,主要检查轴向、径向的轮廓间隙,和支架的安装孔大小及空间位置,从而确定出安装方式和设计方案。
⑵ 根据确定出的安装位置,将制动钳模拟安装在转向节总成的三维模型上。
⑶ 在转向节极限转向、减振弹簧在空、满载的位置(即极限拉、压位置)、摩擦片全新、摩擦片全部磨损等状态下,检验制动钳的空间位置是否合理,是否有干涉发生,如与制动盘、轮辋、转向节、挡泥板、制动油管等的相对位置。
⑷ 若发现干涉,继续在CATIA中修改相关的部件,并且对其进行最大轮廓计算,复查是否与客户条件产生冲突,最终匹配成功。
3.2.4 制动钳各零件之间间隙配合的研究
根据确定好的安装位置,对其进行一系列的公差计算,计算摩擦片与壳体、支架干涉情况,支架和壳体之间的配合问题,活塞行程与壳体桥部、缸部的配合等。如图9为各车型完成的公差计算之一,它涵盖了各个零件之间的配合问题,考虑到了制动钳工作的时候零件与零件之间的干涉问题,零件行程是否满足要求等。若发生干涉或不足,需针对其结果进行模型或零部件的修改调整。
就如对于底部过渡圆角设计的活塞,如图10中所示的尺寸Zmin.,称为最小有效密封导向尺寸,即过渡圆角端点到密封圈的重合长度,根据公差计算须保证Zmin=1.9mm。

3.2.5 摩擦片摩擦性能的控制
摩擦片的主要功能在于将轴向的液压力转化为切向的摩擦力。轴向因受其材料的影响,摩擦片通常具有一定的可压缩性。在制动中,它的这一可压缩性应适中,压缩性过于明显时,虽然噪声小,但踏板感觉差,残余力矩高,磨损过快;相反,若材料过硬,不易于压缩,则虽然踏板感觉好,残余力矩小,耐磨损,但振动噪声严重。切向力对摩擦材料而言也可理解为剪切力,由于摩擦材料和摩擦底板间的连接方式使得在一定的剪切力下,摩擦材料可能会从底板上脱落。为了检验并保证摩擦片在受力条件下仍能正常工作,我们通常作摩擦片压缩试验和剪切试验对它的性能加以控制。
压缩性试验是在常温下6次加压至16 MPa,采用一种与该摩擦片相配套的活塞的替代物压在底板上,检测其压缩性。剪切试验如图11所示是施加规定的轴向力至摩擦材料从底板上脱落,读出剪切力的大小,同时目测光滑脱落面积,相关的标准对脱落面积进行评价。
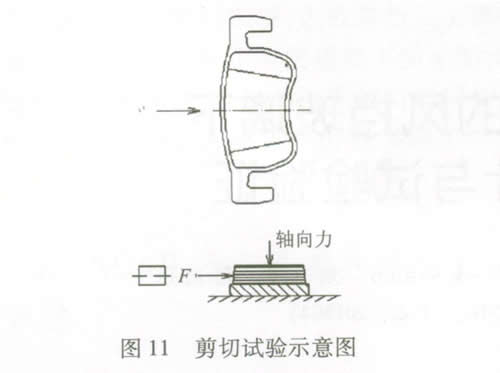
3.2.6 支架上的拉刀槽尺寸精确度的保证
支架上的拉刀槽尺寸的精确度非常重要,如果加工超出规定公差,就会影响壳体移动力,阻碍正常制动。我们在调试完工装后,对生产件通过高度尺及专用夹具进行测量,在生产过程中制作了通止规对其进行100%检验,并且每隔两小时就对其进行抽检,以确保该尺寸满足其精度要求。
3.2.7 自主创新设计噪声优化
不同于国产化产品,FS浮式制动钳是由SABS主导自主开发的新产品,作为公司的一个重要产品系列,应用到现有产品中来,凭借高性能低成本的优势为更多的整车厂服务,占领更多的国内市场。针对不同的客户,项目进行正向开发或匹配开发,以上汽AP11为例,制动钳的造型,经过多次试验、分析、不断的优化和改进,最终达到欧洲对同类产品的要求。其改进优化过程如图12所示。
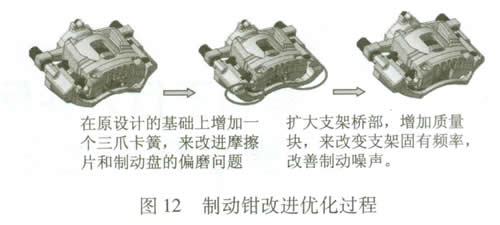
4 结语
该课题在前期研究基础上,充分利用自有技术,在简化结构,降低成本,提高制动效能等方面的研究具有新颖性,并具有较高的实用和市场开发价值。经中国科学院上海科技查新咨询中心分析,该项目综合技术在国内处于领先,并达到国际先进水平。
FS浮式制动钳与国内外同类产品进行分析比较,不仅适应汽车在连续运转、高温、高负载的情况下对制动性能的要求,而且重量轻,构造简单,调整方便,并且降低了材料、能量的消耗,提高了汽车的操作性和舒适性,更能达到技术、质量、成本的统一。