一,目标零排放:采埃孚(ZF)乘用车电驱技术
◆作为一种高效的驱动形式,电驱模块可应用于纯电动小型车、紧凑型车或在混合动力方案中实现后轮电驱
◆轮边电驱动电动扭转梁(eTB)研发项目:扭转梁悬架和驱动电机集成于一套完整系统中,不仅能够提升车辆的动态性能,还优化了车辆的空间设计
◆采埃孚(ZF)研发的电驱技术,兼顾了零排放和操控性方面的设计需求
↑采埃孚(ZF)电驱模块正在进行道路测试:零排放、高输出/重量比带来出色的操控性。
采埃孚(ZF)在传动系统电驱化领域的贡献颇丰:采埃孚(ZF)研发的适用于小型和中型轿车的电动车驱动产品,能很好的适应未来的城市交通状况。
↑位于车桥中间位置的电驱模块,具有120 千瓦的动力输出性能,低速时也能输出高扭矩。
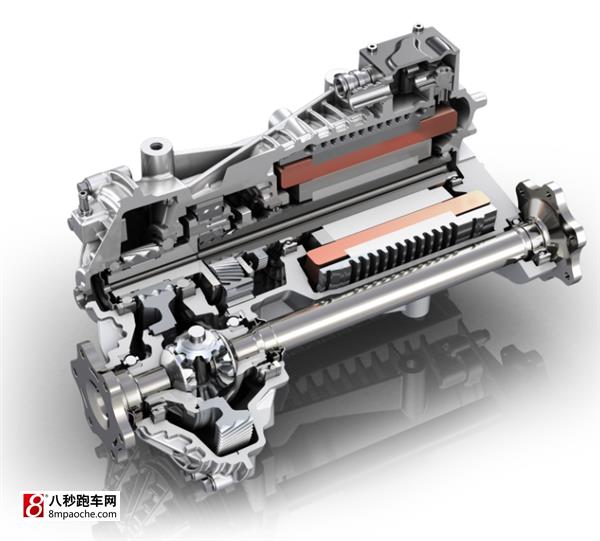
采埃孚(ZF)电驱装置的核心部件是电动马达和一体化的减速单元。
其驱动单元安装于车桥中部,最大输出功率为120千瓦,能保证在低速情况下就能输出高扭矩值。并且,其动力电源是与电驱装置集成为一体的。
采埃孚(ZF)推出了全新配置的驱动概念即功能增强版:电源被集成在电驱桥中,输出功率增至120千瓦。轮边电驱动电动扭转梁(eTB)是采埃孚(ZF)研发的另一项电驱技术,它将半独立悬挂系统与传动系统集成为一体,左右轮各拥有一套紧凑的驱动系统,将变速器和电机集成在一个单独的铝制外壳中。
采埃孚(ZF)的电驱模块的核心是一个异步电机,无需使用带钕或镝等稀有元素的接地材料。此外,这样装置还包括了一个结构紧凑的单速比传动机构、动力电源和一套控制程序。得益于两级减速的传动机构和创新的高转速设计,采埃孚(ZF)电驱系统的转速可达21,000 转/分钟,同时还具备电能转化效率高和性能优异的特点。在车辆刚起步时,电驱系统就可产生17,00 牛·米的扭矩,使车辆可在9 秒内完成百公里加速。该电驱系统的峰值功率为90 千瓦。
电能转化效率高
对于许多纯电动车来说,电动马达和逆变器共同运行在一个特定行驶工况时会产生一定的能量损失,而采埃孚(ZF)推出的电驱装置则解决了这个问题。采埃孚(ZF)通过对整套电驱系统的性能优化,使得电能转换效率提升6%。这款电驱装置的重量约45 公斤,在同等输出产品中设立了重量标杆,而采埃孚(ZF)还在对此不断研发以进一步提升其输出/重量比。
不断提升电机性能
采埃孚(ZF)采用了全新配置的增强版电驱系统:电动马达的输出功率增至120 千瓦和2,500 牛•米的扭矩。集成化的动力电源是这款装置的一大特点。同时,采埃孚(ZF)也在研发适用于各个输出级别的模块化系统,以更好的满足不同客户和车辆的需求。未来,采埃孚(ZF)的电驱系统将不再仅仅适用于小型车和紧凑型车,而将依托车桥混合动力模块,将产品线进一步拓展到中高级别的前轮驱动轿车。
轮边电驱动电动扭转梁(eTB)
轮边电驱动电动扭转梁(eTB)的核心在于半独立悬挂系统与传动系统的集成:左右轮各拥有一套紧凑的驱动系统,将变速器和电机集成在一个单独的轻量化铝制外壳中。另外,利用多面压合连接技术来实现铝制推力杆与钢制横结构的链接,也是这个项目的另一大亮点设计。
↑采埃孚(ZF)系统解决方案:电驱装置使用了性能优化的PUM-X45型逆变器,它结构紧凑,更易于安装于车辆上。
采埃孚(ZF)的这项创新技术是专为微型车和小型车研发的。其单个电机装置可提供40 千瓦的动力,总输出动力为80 千瓦。如果需要额外安装第三个电机,其对装载空间的要求与原先相同。两个独立的驱动电机,可以更精确地为单个车轮分配扭矩,从而增强车辆安全性,提升车辆操纵性能。轮边电驱动电动扭转梁(eTB)的设计沿袭了采埃孚(ZF)中央电驱模块的轻量化和高速设计。同时,电机的装载方式对车辆的非簧载质量不会产生明显的影响。
↑轮边电驱动电动扭转梁(eTB)是专门针对微型车和小型车所研发的一款产品
轮边电驱动电动扭转梁(eTB)的集成化设计有效节约了安装空间。例如,中央电机直接固定在车体上,不再需要额外的机械驱动部件,因此有效释放了车辆中央的装载空间,为汽车制造商们进行个性化的设计提供发挥的空间。这套装置与车身的连接点与传统的车桥系统相似,因而可以轻松实现与现有的技术模块的对接,此外,它也可以匹配传统车型所用的制动系统和标准轮彀尺寸。
二,应用于底盘的采埃孚(ZF) 轻量化技术
◆替代材料和全新设计以及先进的生产方法减轻了零部件重量
◆采埃孚(ZF) 批量生产轻量化零部件已有多年
◆纤维增强性塑料的使用愈加广泛
要降低车辆能耗,轻量化设计是关键技术。对于乘用车底盘,采埃孚(ZF)研发出了一些可互相补充:工程技术致力于零部件的结构优化和功能嵌入。此外,使用了诸如铝和碳纤维增强性塑料 (CRP) 或玻璃纤维增强性塑料 (GRP) 等替代材料,并采用了先进的生产流程。因此,采埃孚(ZF)减少了控制臂、转向横拉杆、悬架支承、减振器和整个车桥系统的重量。
由于减重后可增加车辆续航里程,从而获得更高的接受度,乘用车底盘减重不仅在电动车中是非常重要的,对于所有车辆来说都是很有优势的。
在传统型驱动的乘用车中,可以降低能耗和 CO
2 排放量。同时,簧下重量减轻后,驾驶动力更足,舒适度和安全性也得到提高。飞跃性的革新要归功于智能的轻量化设计。
达成目标的几种方式
因此,对于一件产品,采埃孚(ZF) 采用了多种措施和方法在底盘技术中实现重量优化。其中,材料扮演了关键角色,如正确的材料混合。除了铝和高强度钢以外,采埃孚(ZF) 越来越多地使用一种纤维增强塑料(FRP) 的混合材料。在用这种混合材料设计部件时,采埃孚(ZF) 的工程师们必须开辟新的道路,以最好地利用最高的纤维属性并根据车辆相应荷载和压力调整纤维的方向。以生产为导向的零部件设计连同功能嵌入以及结构优化一起节省材料和重量,进而使该方法成为轻量化工程的基本要素。
为了实现嵌入性功能,多个部件或部件功能被整合在一起。目前,嵌入性的产品已经成为采埃孚(ZF) 产品组合中的一部分。通过嵌入性功能以及替代性材料或新的生产方法还能挖掘额外的减重潜力。
采埃孚(ZF) 轻量化技术
采埃孚(ZF) 轻量化产品范围涵盖从单个底盘部件到整个车桥系统,其特色往往在于集中结合了多种轻量化措施的单个部件。即使是单个较小的乘用车部件产生较少的减重,但加起来也能使整辆车产生显著的减重效果。
↑通过嵌入功能实现轻量化设计:创新性的 SMiCA(集成式球铰链钣金控制臂)不需要接合材料
SMiCA(集成式球铰链钣金控制臂)证明采埃孚(ZF) 已经在提供成熟的轻量化解决方案。控制臂不需要铆钉或螺栓连接,因此比传统的钣金控制臂轻达 23%。此外,它需要更少的安装空间,并在设计底盘时允许更多的设计自由。
凭借纤维增强复合材料和注塑模具制成的轻量化制动踏板进入批量生产,采埃孚(ZF)展示了相较于标准钢制制动踏板,在不降低负荷能力的同时如何减重高达50%。纤维增强复合材料是连续性的、纤维增强的热塑性塑料。材料强度和硬度高,且完全可回收。
↑配有铝制外管的轻量化减振器批量生产已经有多年了。BMW 将它用在多个 M 系车型中
配有铝制外筒的轻量化减振器已量产多年。另外,采埃孚(ZF) 轻量化设计的铝制减振器和采埃孚(ZF)钢制轻量化悬架支承也即将进行批量生产。用于后桥的铝制轻量化减振器是铝制/塑料混合设计的单管减振器,对于它来说,有可能实现最高 25% 的减重。用于前桥的钢制轻量化悬架支撑包括一个钢/塑料制混合弹簧座和一个空心活塞杆,以及管壁强度不同的外筒。在有功能要求的地方,材料进行了加固,其它区域则尽可能得薄。这样能最高减重 20%。
如果没有成功地采用该创新性接合技术,铝制轻量化减振器和钢制轻量化悬架支承的减重是无法实现的。
轻量化设计更进一步
然而,采埃孚(ZF)的轻量化专业性不止于现今已成熟的产品或即将批量生产的产品。采埃孚(ZF) 通过众多理念将乘用车底盘中的轻量化技术进行了进一步的开发。
↑在采埃孚(ZF)轻量化车桥中,带车轮导向的横置板簧承担转向和悬架功能(纵向弹跳及横向摇摆)
一个例子是轻量化悬架支承和转向节模块理念。对于该部件,采埃孚(ZF) 使用了 FRP,即铝和高强度钢的混合材料。通过采用采埃孚(ZF) 理念减重最高可达40%,与传统钢制设计相比重量几乎减半。
采埃孚(ZF)开发的乘用车后桥配备了玻璃纤维增强性塑料制成的带车轮导向的横置板簧,加强了公司用轻量化材料制造完整车桥系统的专业知识。与传统钢制后桥相比减重最高可达 15% 并不是该技术的唯一优势:与复杂的多连杆理念相比,单个部件 ——车轮导向的横置板簧承担了车轮导向、减少车身跳动和横向摇摆等任务。该一体化的部件降低了车桥的复杂性,使 OEM 的安装更为简单,而且节省了安装空间。此外,部件越少意味着重量越轻。
在位于德国施韦因富特市的采埃孚(ZF) 复合材料技术中心致力于开发FRP 材料批量生产过程的技术,目的是为实现诸多轻量化技术理念的开发以及走向成熟铺路。